Undoubtedly, the pharmaceutical industry has been one of the leading ones in recent years,especially following Covid-19 pandemic, which not only has greatly increased the medicines’ consumption of , but also customers’ pharmaceutical awareness.
In fact, in the last 20 years the revenues of the Pharma market have increased from an initial value of 391 Billions $ in 2001 and reaching 1265 Billions $ in 2020.
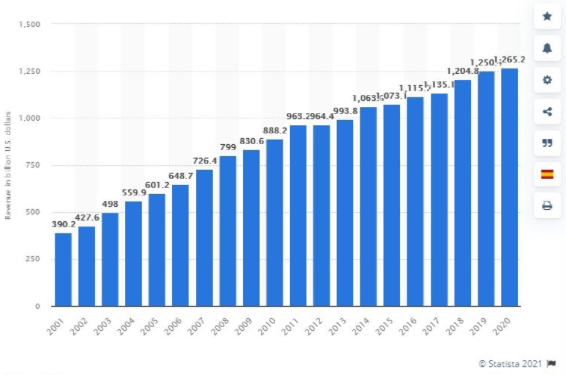
The data is even more encouraging for the future as a compound annual growth rate (CAGR) of 11.34% is expected from 2021 to 2028.
The FDA (Food and Drug Administration, the US government’s agency for drug approval) approved 59 drugs in 2018, 49 drugs in 2019 and 15 drugs until April 2020. In addition, a large number of ongoing clinical trials have created numerous opportunities for market growth.
The retail segment accounted for the largest revenue share, adding to 77.95% in 2020. With rising medical costs and health insurance, more and more people lean towards self-medication as a treatment for minor health problems. The remaining 22.05% represents a non-retail channel.
The Pharma market is experiencing such rapid growth, that new tools and competitive advantages are necessary in order to allow differentiation, while also enhancing the future development.
The focus of this article regards the competitive advantage, which outpaces rivals on industrial results, thanks to the use of custom-made pneumatic cylinders, which significantly increase productivity.
The company we are talking about has designed extremely delicate single-dose bottles that no standard pneumatic cylinder could seal as the minimum pressure of 1 bar would break the package.
Our engineers had to specifically design a cylinder with a soft touch, equal to 0.1 bar (decibar) and also a special amortization mechanism.
Find out more by reading the whole case study.
Table of contents
An in detail and specific needs based market
In the Pharma industry, The production machines constantly face very delicate challenges e.g. working environments that require extreme cleannes, as for the constant contact with delicate and fragile products, which require extreme precision through custom-made components…for processing.
Our client had an unforeseen and unresolved need for pneumatic cylinders.
The challenge involved an experimental project, namely the construction of a single-dose medicinal production machine, targeting either the children and the elderly. More specifically, single-dose disposable straws, including closure caps, were produced for an extremely quick use and low-environmental impact.
A standard cylinder, usually working at too high pressures, could not efficiently compress and create such specific and precise applications, which required a well-calibrated force to avoid splitting the straw.
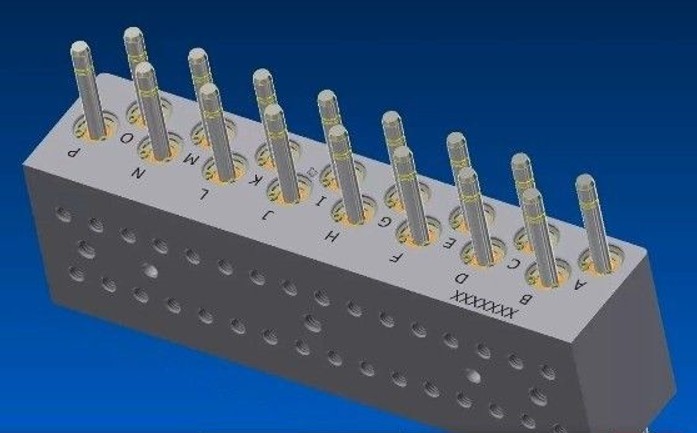
This project required several special and demanding tests,leaving no margin for errors.
The goal was obtaining a series of constant, low-pressure operating cylinders. The tolerance was of +/- 0.05 bar.
An unprecedented special cylinder
Here is a simplified overview of the process.
Each block consists of 16 very compact cylinders, each single one of which must produce a straw, therefore, for every operation the cylinder must produce multiple units simultaneously.
While the upper block presses the cap in place performing the machining, the lower block acts as a support for straws cushioning and containing any excess of pressure.
Each cylinder acts independently and the total dimensions of the block is constantly checked so as to obtain the maximum yield in the minimum space.
To make the cylinder suitable for the pharmaceutical industry, FDA-certified low friction seals and lubricants, stainless steel rods and seegers were implemented in the process.
The toughest challenge emerged during the selection of the components and couplings that could provide the correct level of friction with constancy and repeatability, as this required a lot of attention and hours of work to obtain a perfect balance.
As a pneumatic cylinder usually works between 1 and 10 bar, it comes with no surprise that it takes a huge effort to reduce the operating pressure the closest as possible to 0.1 bar. Such extremely low values on very small cylinders, is made more complex by a guaranteed repeatability of several, while also requiring an incredible series of careful studies, high-end precision and an accurate set of tests on different materials and components.
The key features of the final product were: low friction, the compactness of the individual cylinders and the testing of each individual unit (something not obvious in the world of pneumatics).
Stable and long-lasting cooperation
This latest collaboration and the resolution of this complicated project show how Cy.Pag., mindful of the experience and the skills acquired in numerous tailor-made projects, is capable and versatile in solving most pneumatics-related issues; our motto is consistency, determination and hard work.
The project required weeks of work and continuous testing, in order to achieve the perfect solution.
Our company’s skills and experience not only range in the industrial sector, but in many other areas, which we described in previous Case Studies,always available in our constantly-innovative Blog.
In case you are searching for an in-detail or specific solution to spark your project, especially in the custom pneumatic cylinder industry, do not hesitate to contact us by writing an email to info@cypag.com or call us on +39 0342 60 50 11.