The textile machinery market is constantly and rapidly evolving, with innovations constantly bringing from small to large benefits to the sector’s manufacturers.
Machine manufacturers cannot afford lagging behind and risk succumbing to competition: innovation is the key to survival.
Taking an overview of the most recent sales data for what concerns the index of orders for textile machines developed by ACIMIT, raises some interesting facts. In fact, the association of Italian manufacturers’ data shows that duringJanuary-March 2021’s quarter, the sales increased by 66% compared to the previous year.
As shown in the graph below, after years of constant growth from 2012 to 2017, with the market showing excellent numbers, the trend eventually reversed from 2018 onwards.
Even in such harsh circumstances, our customers have been able to maintain valuable market shares thanks to the competitive advantage of the pneumatic components.
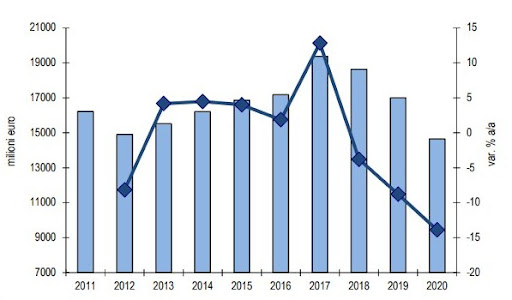
This result was achieved thanks to the good performance of orders collection, either abroad and in Italy.
For the 2021’s situation on foreign markets, the increase was 68%, whereas on the Italian market the growth was more contained, but still interesting (+54% compared to the first quarter of 2020).
This growth has been due to the result of a strong post-Covid-19 recovery market, but also to the market’s partial adaptation to the shock caused by the pandemic; it is seemingly to rise back to pre-2020 levels, if not higher.
Therefore,whether you are an entrepreneur or a manufacturer of textile machinery, the time has come to keep up-to-date with the innovative process and ride the wave of recovery not to be surpassed by your competitors.
Tabella dei Contenuti
Production issues in the textile industry
Today’s success story is about a company, manufacturer of machines for processing (texturing) nylon, often used for the production of women’s socks.
These machines are set to work one wire at a time: each single spool is placed on the spindle and spun at very high speeds, (up to 18,000 rpm.)
Such a process is very important for the final result of the yarn, as the constant tension allows the processing to be carried out without damaging the fabric.
In case of voltage drops, especially the most drastic ones, the machines stop and the production block occurs. On the other hand, whenever the tension is too high, the thread risks being damaged or even broken.
From this analysis, it appears clear how the constant and very precise voltage monitoring performed is essential.
The innovation is also pneumatic
When building a high-speed rotary system, sustained by a pneumatic system that would allow the nylon reel to be changed in a completely automated way, avoiding interruptions,takes manu hours. Hard work and constant and effective communication between Cy.Pag. and the machine manufacturer is crucial.
The final product had to be something new, revolutionary, different from everything that was standard or previously seen.
Firstly, meetings were held, as well as frequent email exchanges to order traceability and field overviews, in order for our engineers to understand the machine’s operation and the customer’s needs.
Then, Cy.Pag. started the design of a totally new cylinder, which we will analyze in-detail below.
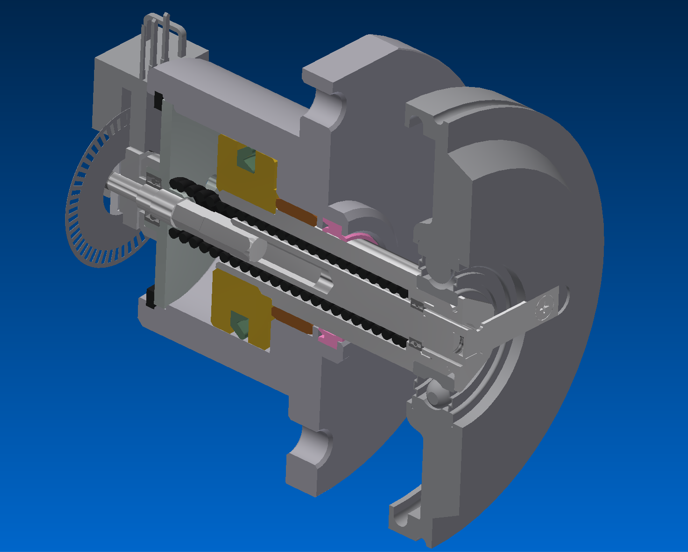
The first cylinder acts as a spindle, with a quick release system for the exhausted reel. It was developed over twenty years ago; however, it has been continuously used to this day to produce hundreds of texturizing machines.
As you might have guessed, the celerity in changing the reel plays a fundamental role, and allows to maintain continuous production, where the pneumatic cylinder’s speed is crucial compared to other types of actuators.
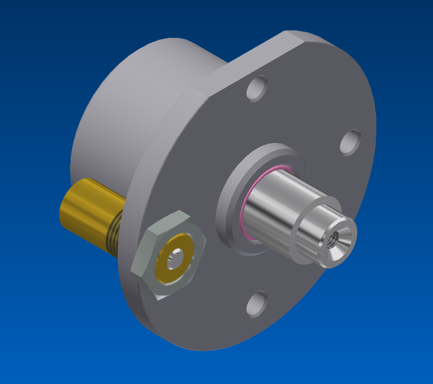
There are other very important aspects of the system to take into consideration.
The spindle must be extremely compact in relation to the axial dimension. This allows the machine’s dimension reduction and several consequent economic advantages.
Another important aspect is the spindle guide’s precision.
The texturizer (produced by a leading company worldwide), is characterized by extremely high operating speeds which are reflected in the unwinding of the reels at over 18,000 rpm.
The pneumatic spindle must therefore rotate at such speeds without introducing oscillations due to eccentricity, while supporting the high vibrations created by the irregularities in the shape of the wire spool. Its design was created to ensure the maximum possible alignment, regardless of the compact size.
The success of the project has ensured a constantly-evolving working relationship of more than twenty years.
A product permanently evolving
As time passed and the field tests intensified,the new cylinder required more attention.
The texturing machines’ market technological evolution has led to the need of increased control over the speed of unwinding and rewinding of the reels.
The regulation of speeds and tensions makes it possible to increase production rates, and at the same time to reduce downtimes (thread breakage). Moreover an improved control over the winding of the threads on the spools prevents further machine stops.
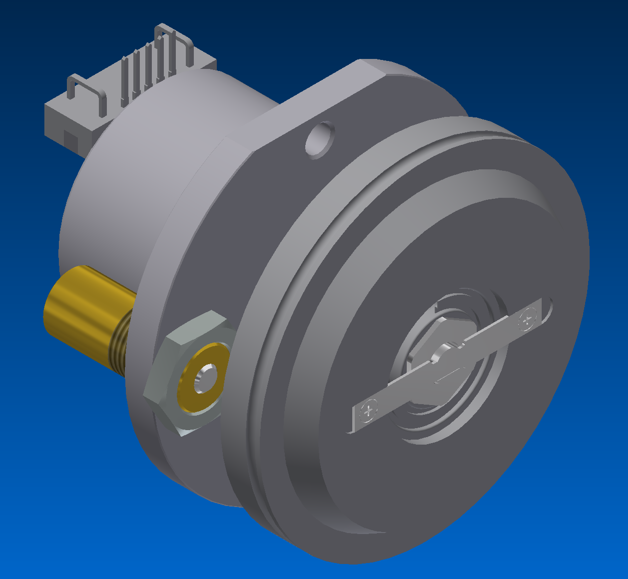
This need has turned into a request by the customer who requested a shaft on the opposite side to the rotating flange, in order to transmit the rotation of the flange itself, and therefore of the spool. This would allow the assembly of an encoder, utilized to read in real time the angular position of the spool.
All this should have been combined with a further reduction of the total length of the tailstock, to house the encoder without increasing the size of the machines.
The final goal was achieved by applying two coaxial shafts to the cylinder’s rod to allow the transmission of the rotary motion as well as the rod extension and the return movement.
All this was achieved without creating noteworthy eccentricities that destabilized the tailstock and without reducing the resistance to oscillations caused by the spool.
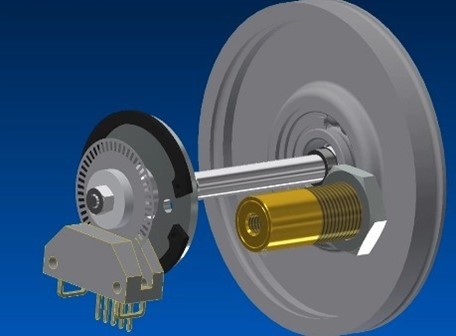
The extremely high stress put on the miniaturized connecting elements, required the use of high-strength elements, made of hardened steel to guarantee the minimum service life.
The customers feedback on the test confirmed the full satisfaction of the initial requests.
Optimization to create value
The optimization of our custom projects over time is one of Cy.Pag. ‘s core strengths, which not only creates value for the customer in a given historical moment, but also makes improvements that allow us to maintain the competitive advantages over time.
In fact, we try to establish a strong and long-lasting bond, by fully supporting our customers’s requests and needs, and by helping them find the most effective, specific solutions.
The case study I have just described has allowed textile machinery’s manufacturers to dispose of a final product of the highest quality, also thanks to our custom-made cylinders.
The main advantages that this solution has brought are: reliability and robustness (which are constants that we always look for in our custom-made projects), work’s speed execution and control of the application.
In our Blog you will find many Case Studies in different industrial sectors for you to have an overview on our success stories and learn how we have helped so many entrepreneurs to create a market and a competitive advantage over their competition.
Request a free consultation for your company now by calling +39 0342 60 50 11 or by writing an email with your specific needs to info@cypag.com. We will be at your complete disposal for any technical analysis required.