The areas intended for animal breeding require a product capable of withstanding the corrosiveness of the environments, not only due to the animal excrement toxicity, but also the constant use of very aggressive detergents for the machines’ washes.
Today’s standard cylinders are the result of the ’70s’ plannings: these cylinders are considered a masterkey and are indistinctly used for every application regardless of possible specific adaptations, which might improve their performance, either in terms of durability and reliability.
This leads to more frequent maintenance, even replacement, in order to reduce the negative impact of a machine block.
For these practical reasons pneumatic cylinders intended for this usage require, always more, greater reliability and durability.
What makes the manufacture of a specific custom cylinder for corrosive environments so complicated?
To better analyse the common issues occuring in the making of such a cylinder, let us closely and attentively look at the story of a company specialised in the animals’ breeding (cattle to be precise) for the production of dairy products.
The company uses machines which are constantly in direct contact with corrosive chemicals, therefore subject to frequent washings and a high-rate replacement of cylinders. According to the size of the industry, hundreds of cylinders might be replaced every year.
It is relevant to take into consideration the shift that allowed the use of customized cylinders, since it brought significant added value to the customer ever since it was applied.
Table of contents
Common issues of standard cylinders in corrosive environments
In this type of industry, the working environment is extremely dirty and cankerous due to the gases and the cows’ wastes
Not only is the cylinder used to clean and sanitise dairy cattle, but also to open and close the metal bars in order to facilitate the animals’ entrance and to keep them still during washing procedures.
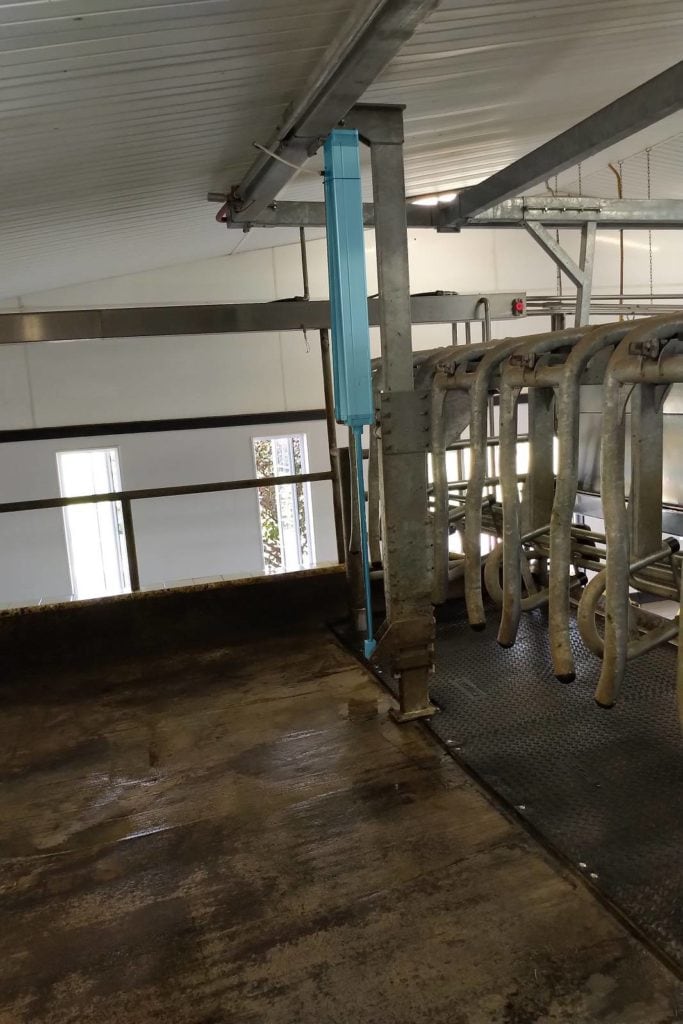
The application is rather simple. The pneumatic cylinder is activated by a controller which raises the metal cage, keeping the animal still for a proper washing and to make the process as minimally-intrusive as possible.
As late as 2019, standard cylinders were default either in terms of design and materials used. This option involved a traditional NFPA cylinder with exposed rods.
This type of cylinder blocked the majority of the animals’ dirt in gaps between tube and tie rods, complicating the washing and causing severe corrosion.
Seeing the dirty environment described before, automated system’s washing is common.
In order to thoroughly clean the whole system, chemical agents and detergents (especially aggressive ones) are often used, which obviously further the cylinder’s body corrosion, but also the piston rod and gaskets’ one, shortening even more their usability span.
Main consequences are a periodical replacement of both pistons and cylinders. Cost of materials and maintenance frequency considered, the customers’ perception of the machinery was of poor quality.
The toughest challenge: reliability and durability increase
Farmers and general users of the machinery only stressed one point: a longer span of usage and a drastic reduction or even a minimisation of the number of interventions required to solve a machine blockage or issues. Simply put, they demanded product reliability.
To achieve this, two main issues were to be solved:
The most commonly used system that required too much maintenance and excessive costs for materials and working hours
The cylinder manufacturer provider was unable to promptly solve the machine builder’s problems and to prevent them
This situation perdured over the years to such an extent that farmers almost resigned to sustain the huge maintenance and replacement costs for pneumatic cylinders.
To sum it up, no machine manufacturer had yet perceived the excellent chance offered by such a problem: creating an innovative, cheaper and more competitive solution.
At the time Investing in R&D to find a solution was economically exhausting and unaffordable.
Not to mention, who would have risked investing into an unknown product, with little to none development perspectives?
In fact, such an investment would have created many problems for machine manufacturers, who already had to deal with unsatisfied customers on one hand and found themselves facing an insurmountable hindrance, due to the lack of know-how and interest from component suppliers on the other.
There was only one fact: the standard cylinder was not the right answer.
This stalled situation started to move forward when a machine manufacturer, specialized in animal cleaning equipment, requested a custom-made cylinder, which had to be either suitable for such a working environment and not be too aggressively affected by the corrosiveness of the animal’s washing procedures and manure.
How to design a hyper-resistant cylinder?
The continuous problems occurring on the systems allowed an opportunity to grow: realising first and seizing the opportunity later, an in-depth analysis was carried out, which balanced either the system functioning and of all the main causes of the malfunction.
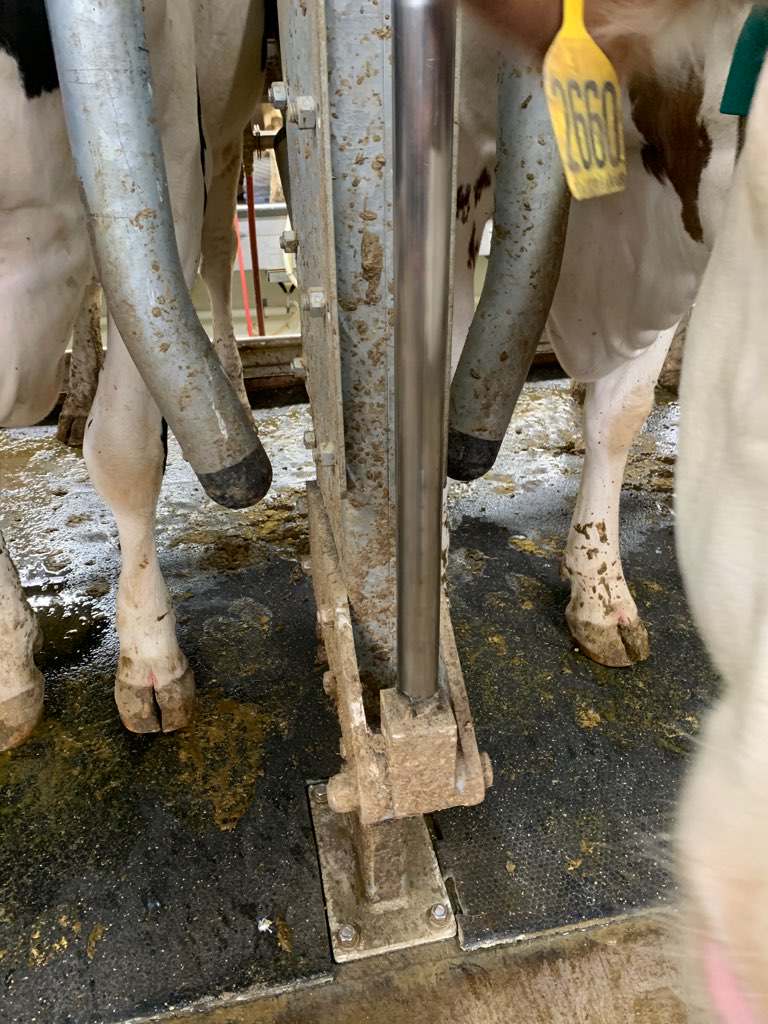
An obvious fact and the main issue outlined was the constant presence of a consistent quantity of corrosive and occlusive material (animal manure and/or soil). Moreover, the frequent washings and the use of chemicals, as previously mentioned, corroded the cylinder and piston’s materials components.
The first step was to measure the existing system at the time and to understand its boundaries in order to design a proper and brand-new custom cylinder that would fit perfectly with the existing system, without having to revolutionize it from scratch, thus avoiding inconvenience for both manufacturers and end users.
The biggest challenge was to build a product capable of working as well as its predecessor, but with a much higher reliability and corrosion resistance.
To summarize:
On the one hand we have a driven-in the field company, capable of analyzing and managing customer’s needs
On the other hand we have a company specialized in the design of customized cylinders, with a dedicated technical department, with an advanced and practical know-how for the creation of ultimate technical solutions
This was the situation at the start of the collaboration and it led to a fundamental choice towards the success of the project: the creation of a clean profile cylinder, neat and grooveless, to avoid dirt settling and consequent corrosion of the material and the life span and performance reduction and of the cylinder itself.
In addition, the customer’s needs once evaluated, the materials choice fell on a stainless steel rod with high resistance seals to tackle corrosion. All this without compromising the cylinder’s functionality.
To be completely honest, the best solution would have been a totally stainless steel cylinder, but its cost is out of the market’s range.
The clean profile is therefore an excellent compromise between quality and price: it avoids large dirt sediments that might cause local piercing corrosion on one side, and guarantees a good resistance to corrosion thanks to the excellent quality of the hard oxidized tubes, on the other.
A turning point for breeders
After months of testing on the field, the customer was finally able to see and experience first hand, the several benefits brought by the new solution, tailored for this type of application.
First of all, the new clean and neat profile was one of the best improvements: this choice made the maintenance and cleaning process much easier for the technician and also implied fewer problems for the cylinder, freed of the sedimented material and more resistant to the washings thanks to the newly and carefully selected materials chosen during its construction.
The game changer in this evolution was the previous experience of our technical department and the client company, which promptly identified the best solution.
This knowledge and expertise in the field derives and results from years of practice and sperimentaiton with similar applications, which consequently led to a versatile product: adaptable to to pre-existing machines and made by easily interchangeable elements that could be easily assembled and disassembled on the system.
Not only has this technological development brought technical benefits, but also economical ones. In fact, the choice of a clean profile, free from tie rods, meant fewer materials usage and less complex production processes, which significantly lowered production’s costs.
Therefore, the result was a better and more efficient product either from a mechanical point of view and from an economical one, thanks to the reduction of costs for manufacturers, who even increased their revenues.
The only complaint we received was that “the cylinders lasted too long”! In fact, after 2 years of usage, the customers discovered that the life span of the components was up to 60% longer.
A long term partnership
Undoubtedly this collaboration brogut and will bring mutual hardly beatable leverages, also innovating and enhancing tailor-made solutions for non-standard applications.
The ultra-competitive leverage will be the result of a development process perfected over time and, thanks to the solid bonds that are being built within customer and service provider. We will also bring more and more reliable products on the market that are perceived as of high-quality and efficiency by both the end customers and machine manufacturers.
In fact, this product has revolutionised the industry, replacing all the old cylinders, largely due to customer’s word of mouth and the communication skills of Cy.Pag.’s partner company.
This was certainly an excellent starting point for two realities sharing the desire to innovate and bring end customer-satisfactory solutions, with a particular attention to details of quality, costs of production containment and management.
Cy.Pag. tailored a structured and tested process for the collaboration with companies/distributors, which allows the development of specific solutions, adaptable to the individual needs of each customer or industry of application.
After years of experience and improvements with over 5,000 custom cylinders designed and efficient on field, this expertise is accessible to all machine builders who have a very innovative or ambitious project, but cannot realize it due to the limitations of standard pneumatic cylinders.
To have a free evaluation by one of our specialized technicians and a report including the main specific benefits of the tailored solution provided to you, please contact us at +39 0342 60 50 11, or send us an email to info@cypag.com.