Le aree destinate all’allevamento degli animali, richiedono soluzioni capaci di sopportare la corrosività degli ambienti, a causa della presenza di escrementi degli animali, ma soprattutto dei frequenti lavaggi delle macchine con detergenti molto aggressivi.
I cilindri standard, come li conosciamo oggi, sono frutto delle progettazioni degli anni ’70: questi cilindri sono come un passpartout e vengono indiscriminatamente installati in ogni applicazione senza adattamenti specifici, che ne migliorino le performance, in questo caso in termini di durabilità ed affidabilità.
Ciò comporta una necessità frequente di manutenzione, e ricambio, per ridurre l’impatto negativo di un blocco macchina.
Ecco perché i cilindri pneumatici destinati a questa applicazione necessitano di una maggiore affidabilità e durabilità.
Ma perché costruire un cilindro personalizzato per ambienti corrosivi è così complicato?
In questo caso specifico andremo a vedere la storia di un’azienda che lavora nel settore dell’allevamento di animali, nello specifico di bovini, per la produzione dei derivati del latte.
In questa azienda, sono presenti macchine sottoposte al contatto con agenti corrosivi, e soggette a lavaggi molto frequenti, che comportano il ricambio di cilindri con una frequenza molto elevata: in base alle dimensioni dell’industria si possono arrivare a sostituire anche centinaia di cilindri all’anno.
Analizziamo insieme perché si è passati dall’utilizzo di cilindri standard a quello di cilindri su misura, portando un notevole valore aggiunto al cliente.
Tabella dei Contenuti
I problemi dei cilindri standard in ambienti corrosivi
In questo tipo di industria l’ambiente di lavoro è molto sporco e corrosivo: conseguenza dei gas e del letame prodotto dalle mucche.
Il cilindro viene utilizzato in un impianto che pulisce e disinfetta le mucche da latte ed ha la funzione di aprire e chiudere le sbarre metalliche per favorire l’ingresso degli animali e mantenerli in posizione durante il lavaggio.
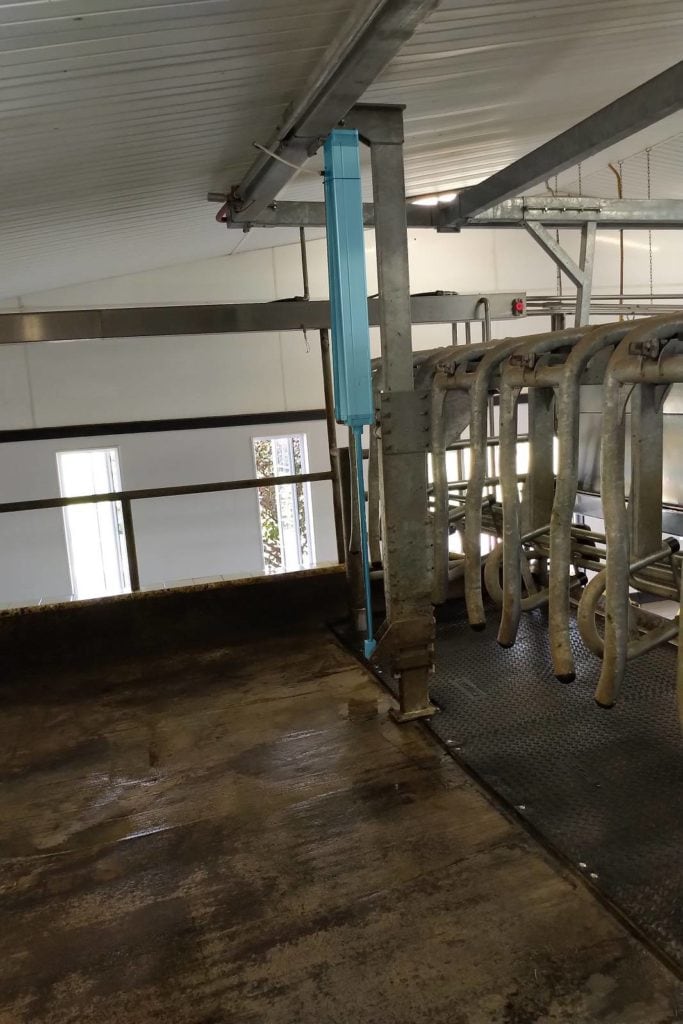
L’applicazione, quindi, è molto semplice. Un comando aziona il cilindro pneumatico che permette di sollevare la gabbia metallica, che mantiene l’animale in posizione per il corretto lavaggio e per rendere il processo il meno fastidioso possibile.
Fino a poco tempo fa, parliamo del 2019, venivano utilizzati dei cilindri standard sia sotto il punto di vista della progettazione che dei materiali utilizzati. Questa soluzione prevedeva un tradizionale cilindro NFPA a tiranti scoperti.
Questo cilindro raccoglieva tutta la sporcizia degli animali negli interstizi tra tubo e tiranti, rendendone difficoltoso il lavaggio e causando fenomeni corrosivi molto gravi.
Essendoci, come abbiamo descritto, un ambiente molto sporco, vengono effettuati dei lavaggi automatizzati dell’impianto.
Per poter pulire in modo efficace tutto il sistema sono frequentemente utilizzati anche degli agenti chimici e dei detergenti (anche molto aggressivi), che ovviamente favoriscono ulteriormente la corrosione, non solo del corpo cilindro, ma soprattutto dello stelo e delle guarnizioni, accorciando ulteriormente la loro vita.
Risultato di tutto questo: periodicamente i pistoni o i cilindri dovevano essere sostituiti. Considerando il costo dei materiali e il grosso costo della manutenzione frequente, i clienti percepivano una scarsa qualità dei macchinari.
La sfida più complessa: aumentare l’affidabilità e la durata
Gli allevatori ed utilizzatori finali degli impianti chiedevano solo una cosa: poter lavorare con una certa continuità, senza dover intervenire frequentemente per risolvere un blocco macchina o per prevenirlo. In una sola parola, volevano l’affidabilità del prodotto.
Per ottenerla c’erano due grossi problemi a cui far fronte:
Il cliente aveva un impianto che richiedeva troppa manutenzione, con costi elevati per i materiali e le ore di lavoro
Il produttore di cilindri dal quale si rifornivano non era in grado di rispondere ai problemi ed alle sfide del costruttore di macchine
Questa situazione si è trascinata negli anni, tanto che gli allevatori si erano rassegnati a dover sostenere continui costi di manutenzione e ricambio dei cilindri pneumatici.
Insomma, nessun costruttore di macchine sembrava aver ancora percepito l’opportunità che si nascondeva dietro un simile problema, quella di creare una soluzione innovativa e competitiva.
Investire in Ricerca & Sviluppo per trovare una soluzione, era difficile, ma soprattutto molto costoso.
Chi avrebbe mai investito con prospettive di sviluppo ignote?
Infatti, una simile scelta avrebbe creato non pochi problemi ai costruttori di macchine, che da un lato avevano dei clienti insoddisfatti per i motivi sopra citati e dall’altro si trovavano di fronte ad un muro insormontabile, dovuto alla mancanza di know-how e di interesse da parte del fornitore di componenti.
La certezza era una sola: il cilindro standard non era la risposta giusta.
Questa situazione si è interrotta nel momento in cui, un costruttore di macchine specializzato in impianti di pulizia di animali, ha deciso di incaricarci della progettazione di un cilindro su misura adatto per questo ambiente di lavoro e che non subisse in modo troppo aggressivo la corrosività dei lavaggi e del letame degli animali.
Come si progetta un cilindro Super Resistente?
I continui problemi che si verificavano sugli impianti, hanno fatto nascere un’opportunità: prendendo la palla al balzo è stata fatta un’analisi del funzionamento dell’impianto e di tutte le cause del malfunzionamento.
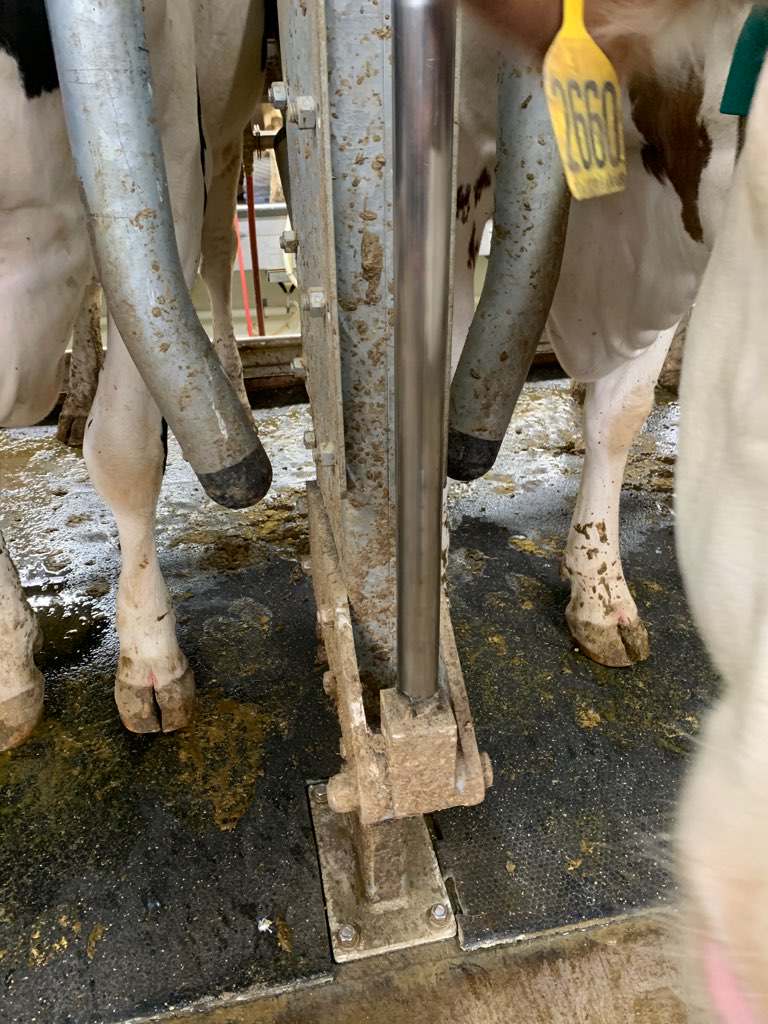
É saltato subito all’occhio che il problema cardine era la presenza di molto materiale corrosivo ed occlusivo (il letame degli animali e/o terra). Inoltre i frequenti lavaggi e l’uso di agenti chimici, come già visto, corrodevano molto velocemente i materiali che componevano cilindro e pistone.
Il primo passo è stato quello di prendere le misure dell’impianto esistente e capire quali fossero i margini di manovra per progettare un nuovo cilindro custom che calzasse a pennello con l’impianto esistente, senza doverlo rivoluzionare, andando di conseguenza a creare un disagio ai produttori ed agli utilizzatori finali.
La sfida risiedeva nel costruire un prodotto con le stesse capacità di lavoro del suo predecessore, ma con un’affidabilità ed una resistenza alla corrosione molto superiori.
Per riepilogare:
Da una parte abbiamo un’azienda, con una grande esperienza sul campo, capace di analizzare e gestire i bisogni del cliente
Dall’altra un’azienda specializzata nella progettazione di cilindri su misura, con un ufficio tecnico dotato di un know-how specifico dedicato alla creazione di soluzioni al limite delle prestazioni tecnologiche.
Così è iniziata la collaborazione che ha portato ad una scelta fondamentale per la riuscita del progetto, quella di un cilindro con un profilo pulito, senza scanalature o gole, zone in cui la sporcizia sedimenta e va a corrodere il materiale, compromettendo la vita e le prestazioni del cilindro stesso.
Inoltre, dopo aver analizzato i bisogni del cliente, la scelta dei materiali è virata decisamente su uno stelo in acciaio inossidabile con guarnizioni ad alta resistenza alla corrosione. Tutto questo senza compromettere le funzionalità del cilindro.
In questo caso specifico, la scelta migliore sarebbe stata un cilindro totalmente in acciaio inox, ma questa soluzione sarebbe totalmente fuori mercato.
Il profilo pulito è quindi un ottimo compromesso tra qualità e prezzo: evita grossi sedimenti di sporco che causano localmente corrosione perforante, inoltre, l’ottima qualità dei tubi ossidati duri garantisce una buona resistenza alla corrosione.
La chiave di svolta per gli Allevatori
Dopo mesi di test sul campo il cliente ha potuto osservare e provare sulla sua pelle diversi benefici apportati dalla nuova soluzione costruita su misura per questo tipo di applicazione.
Innanzitutto il profilo pulito della nuova soluzione è stata una delle mosse vincenti: questa scelta ha fatto sì che il processo di manutenzione e pulizia fosse molto più semplice per il manutentore e creasse pochi problemi al cilindro, che non aveva più materiale sedimentato e resisteva ai lavaggi grazie ai nuovi materiali accuratamente selezionati per la costruzione.
In questo, un fattore chiave è stata l’esperienza pregressa del nostro ufficio tecnico e dell’azienda cliente, che ha saputo individuare con rapidità quale fosse la soluzione migliore.
Questa capacità deriva da anni di esperienza in applicazioni simili, grazie ai quali siamo stati in grado di portare un prodotto che si adattasse alle macchine pre-esistenti con degli elementi costruttivi che fossero facilmente montabili e smontabili sull’impianto.
Tutta questa tecnologia, non ha portato solo benefici tecnici, ma anche economici. Infatti aver scelto un profilo pulito senza tiranti, ha fatto si che venissero utilizzati meno materiali e processi produttivi meno complessi, abbassando notevolmente i costi di produzione.
Quindi non solo si è ottenuto un prodotto migliore sotto il punto di vista meccanico, ma anche sotto il profilo economico, con una riduzione dei costi per le aziende produttrici, che hanno potuto aumentare i loro ricavi.
L’unica lamentela che abbiamo ricevuto è stata quella che “i cilindri duravano troppo”! Infatti, dopo 2 anni di utilizzo il cliente ha riscontrato una vita dei componenti più lunga del 60%.
Una Partnership di lungo termine
Sicuramente questa collaborazione ha portato e porterà un vantaggio competitivo ad entrambe le parti, innovando e trovando soluzioni su misura per applicazioni non standard.
Il vantaggio competitivo sarà frutto di un processo di sviluppo consolidato nel tempo e, grazie alle solide basi che si stanno costruendo con il cliente, si porteranno sul mercato prodotti molto affidabili, ma soprattutto con un’alta qualità percepita dai clienti finali e dai costruttori di macchine.
Infatti, questo prodotto ha generato un tale successo che sta sostituendo tutti i vecchi cilindri, in gran parte dovuto al passaparola dei clienti ed alle doti comunicative dell’azienda Partner di Cy.Pag.
Questo è stato sicuramente un ottimo inizio per due realtà che hanno voglia di innovare e portare soluzioni che soddisfino i clienti finali, con una particolare attenzione alla qualità ed ai costi di produzione e gestione.
Cy.Pag. ha messo in campo un processo strutturato e collaudato per la collaborazione con aziende/distributori, che permette di sviluppare soluzioni specifiche, su misura, in base alle singole esigenze di ogni cliente o settore di applicazione.
Dopo anni di esperienza con oltre 5.000 cilindri personalizzati progettati, queste competenze sono accessibili a tutti i costruttori di macchine, che hanno un progetto molto innovativo, ma non possono realizzarlo a causa dei limiti dei cilindri pneumatici standard.
Per avere una valutazione gratuita di un nostro tecnico specializzato ed una relazione con i benefici specifici legati alla soluzione che ti verrà proposta, contattaci al numero +39 0342 60 50 11, oppure scrivi una mail a info@cypag.com.