Always more frequently food contamination is a common topic; by doing so, newspapers and news broadcasts target aggressively those companies that put the safety of consumers at risk.
Have you ever heard of cosmetic contamination though?
As cosmetics are always at contact with the skin and the mucous membranes, they might carry extremely serious infections and microbiological risks.
In fact, also cosmetics have an expiration date, exactly like foods, with an abbreviation on the packaging reporting 3M, 6M, 12M, 18M, 24M or 36M, corresponding to the months of expiry.
The most dangerous part in the manufacturing process is packaging, since any residues that might be stuck in the dosing machines may contain infectious pathogens, such as Staphylococcus (acne and peeling of the skin), Bacillus Cereus (serious eye infections) or Candida (rashes and dermatitis).
Machine manufacturers and maintenance technicians know exactly the risks and have the responsibility to pay close attention to system maintenance, frequent cleaning and preventing unwanted residues from coming into contact with the product to avoid infections to consumers (eg. Shampoos, creams for the face, etc.).
In this sector, such as the food sector, cleaning the environments and the cylinders themselves is essential to stay on the market and avoid possible consumer’s lawsuits.
A practical example, as always, is the best way to illustrate some of the risks and responsibilities involved: a hams production company, not long ago, was about to proceed with a routine operation, namely the hams deboning.
This is a highly mechanized process, which takes place when the meat has not been cured yet.
The procedure behind it takes some steps: batches of hams of around 1,500/2,000 pieces are firstly defrosted, then prepared and need to be processed within a few hours, otherwise they might not respect the edibility standards, as they cannot be put back into the freezer in case of delays.
Before the process, some of the managers observed that the machines were not working properly and this could have prevented the whole process from being completed according to the quality standards. Not being kept fresh in freezers, batches of meat could become contaminated, thus converting them into waste.
This thinking explains why the executives were forced to have every single employee (including the executives themselves) butcher the hams by hand in order to contain the waste, which would increase dramatically in time.
Certainly, in the Beauty industry is hard to work with such perishable materials as meat; nonetheless machine downtimes (in the worst cases) or even delays for maintenance, have a negative impact on both productivity and economics.
In this case of study, we will talk about the analysis that was made on the filling systems, in order to design and then produce custom-made pneumatic cylinders that would drastically reduce maintenance and cleaning times.
Table of contents
How do the pneumatic dosing cylinders work and adapt to the beauty sector?
The function that a pneumatic cylinder must perform on this type of system is as simple as it is delicate.
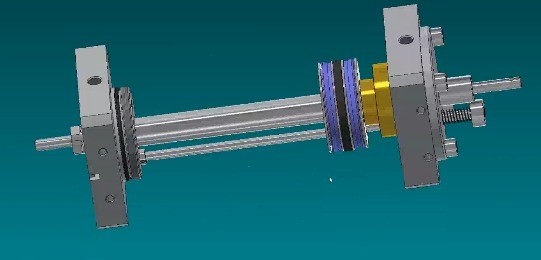
A handlebar adjusts the stroke of the cylinder and allows you to choose the quantity of product to be pumped by the machine to perfectly fill the container.
This is the first operation, to be done before launching the entire system to begin production.
Once the system is started up and activation of compressed air the cylinder comes into operation, each cycle fills the containers of the production line.
To ensure complete sterilization of the work environment, these cylinders require constant maintenance: cleaning and changing the seals, to avoid the deposit of contaminating residues.
The standard cylinder requires relatively long times to be firstly disassembled from its housing, then opened (by unscrewing the tie rods), and finally cleaned thoroughly; then the whole process is repeated in reverse to reassemble everything perfectly.
An 8- cylinders machine requires a large investment in terms of maintenance time, up to the point that it is extremely advantageous and profiting to invest in maintenance process optimization.
Let’s see what were the fundamental steps for the design and production of this type of cylinders.
The challenges: reduce time and costs to increase productivity
In the Food Case Study, (which I invite you to read by clicking here) common issues were malfunctions on the system, especially linked to a cylinder that was not able to achieve the performance required by that application (before bringing an improvement with our solution).
In this study case, the issues were quite different; in fact, there were no major defects in the application of the cylinder itself, which worked perfectly during operation, but that technology made maintenance and cleaning operations really difficult.
It was right about time to innovate and find a way to increase productivity and make life easier for maintainers.
What was the biggest problem that the old machines presented?
As we said before, thorough routine maintenance was performed in this sector.
A large part of the machine had to be disassembled to reach the cylinder screws (located on the back) and replace the gaskets for the cleanup.
This type of operation is very much alike mechanic’s work, when they have to disassemble the water pump which is in an inaccessible position, and then they are forced to pull down the whole engine to complete the job.
The operation required the maintenance technician about 10/15 minutes per cylinder, which is not an extremely high time, but if we consider having to perform it on 8 cylinders per machine, on 10 machines, then time becomes a key factor to be considered.
As already mentioned, it is not a question of machine functionality, but optimizing this process would save working hours exponentially; time saved could also be dedicated to productive tasks while also lowering the costs for the maintenance of the machine itself.
Maintenance must be completed meticulously, as sediments, apart from constituting a risk of contamination, may corrode the cylinder, consequentially causing serious damage and reducing the life of the cylinder.
As we have seen in the case of food industry in the example above, such damage is considerable and the same principle applies to cosmetics producers.
Any part of the cylinder that may favor the sedimentation of the material becomes an area to be maintained frequently and urgently.
In detail, the cylinder tie rods favor the deposit of material and require greater maintenance, precisely due to the special attention that must be paid to eliminate all product sediments/corrosive agents.
A new, easily-to-handle cylinder
When our technical department started designing the new cylinder, it was clear from the start that it would be designed for:
Simplify the life of maintenance workers;
Remove, whether possible, any part that favors the deposit of product/chemical agents on the cylinder.
How could maintenance be simplified without compromising the functionality of the cylinder?
The solution is as simple as it is effective.
After thorough tests, we opted to breaking down the cylinder head into 2 minor components: the central one is removable as a sort of cap by removing 4 easily accessible screws allowing much quicker removal and cleaning of gaskets, with no time wasted.
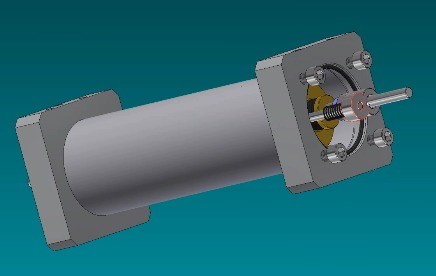
To stress the improvement obtained, let’s compare the 2 maintenance processes:
OLD SYSTEM: it was necessary to disassemble the machine from below, fix it in an uncomfortable position, remove 8 screws in different positions, extract the cylinder, open it and clean and replace the gaskets. After processing, carry out all the steps backwards to reassemble everything. Repeating the operation for each cylinder. Excessive work such as disassembling the motor to change the water pump!
NEW SYSTEM: with the new cylinder, just remove 4 screws, clean and replace the gaskets, and the job is done!
This approach allowed the reduction of maintenance times up to a tenth of the previously required time and increases the frequency, thus improving the performance of the machine and reducing the risk of contamination.
There was a time saving of 20 minutes compared to the actual completion in 2/3 minutes.
As we said earlier, this operation is done not on one, but on several machines: multiplying the time saved by 10 machines we have a total time saved of 2/3 hours on each maintenance operation.
Doing the math, we not only save time, but we can also intervene much faster in the event of a machine block, almost completely removing production delays.
What’s more, concerning the cylinder design and its functionality another choice was taken by our technical department: they removed the tie rods, which greatly favored the accumulation of corrosive material reducing drastically its negative effects.
This choice permitted (as can be seen from the image) the creation of a new cylinder with an extremely minimal design, but with features that make it unique as well as the best choice for this type of application.
The absence of tie rods improves the cleaning efficiency, as that delicate point in which contaminating residues are more commonly found, no longer exists; therefore also the time once dedicated to complex cleaning processes, also disappeared due to this modification.
The conquest of the market
The design strategies and outcomes which resulted in a tie rods-less cylinder with a rapid maintenance system, were greatly appreciated by our customer as they gained a considerable competitive advantage over his competitors, still linked to an obsolete system.
Not only that, the solution was borrowed in other sectors (with similar characteristics), simplifying the maintenance and cleaning processes, and thus saving time to maintenance workers and thousands of euros to entrepreneurs.
It would be reasonable to expect a price growth in our brand-new cylinder model, given the measures taken and analyzed along this study case; however, we managed to maintain the same price, but with much higher benefits.
Any entrepreneur knows that it is worth spending a few extra coins to save thousands of euros, with a huge return on investment.
The partnership that has been created with the customer has lasted for years, with continuously growing product innovations and satisfaction of its end customers.
As a matter of fact, here at Cy.Pag., not only we take care of our direct customers’ needs, but also our customers’ customers ones; we tend to have a long-sight view and we are proud to consider it one of our strengths. This allowed us to become leaders in the production and marketing of customized pneumatic cylinders and to ensure that returns do not exceed 0.46% each year, showing how reliable our products are.
To have an almost unfair competitive advantage, which will see you stand out among your competitors, contact a tyre consultant on +39 0342 60 50 11 or write to info@cypag.com to get a free consultation; we will be more than happy to analyze your specific situation, issues and we will attentively guide you in choosing the most suitable cylinder for you.