Those who produce machines for the Sorting of agricultural products can only imagine how complicated it can be to design and maintain this type of plant.
In fact, it is necessary to assemble extremely advanced technologies, which are therefore rather delicate, with the need to work continuously throughout the season, 24 hours a day, in an highly corrosive environment due to the juices released from agricultural products.
In this case study, we are going to talk about a vegetable sorting machine manufacturer based in Italy with over 1.500 machines installed worldwide. Its turnover and exports are always growing, thanks to innovation and collaborations that have continued over the years with external partners.
Let’s see what successful factors have guided this industry leader to conquer the market.
Table of contents
Why is the standard pneumatic cylinder not suitable for vegetable sorting machines?
Vegetable sorting machines require very high operating speed and frequency, without which it would not be possible to obtain satisfactory results for agricultural producers.
This kind of equipment is dedicated to the control of agri-food products: Fruit and Vegetables. In this case we are talking about an optical sorter with high resolution sensors, which examines the product checking 100% of the surfaces of each of the vegetables inspected and is able to discard color defects, rotten products and foreign bodies even of the same color as the good product.
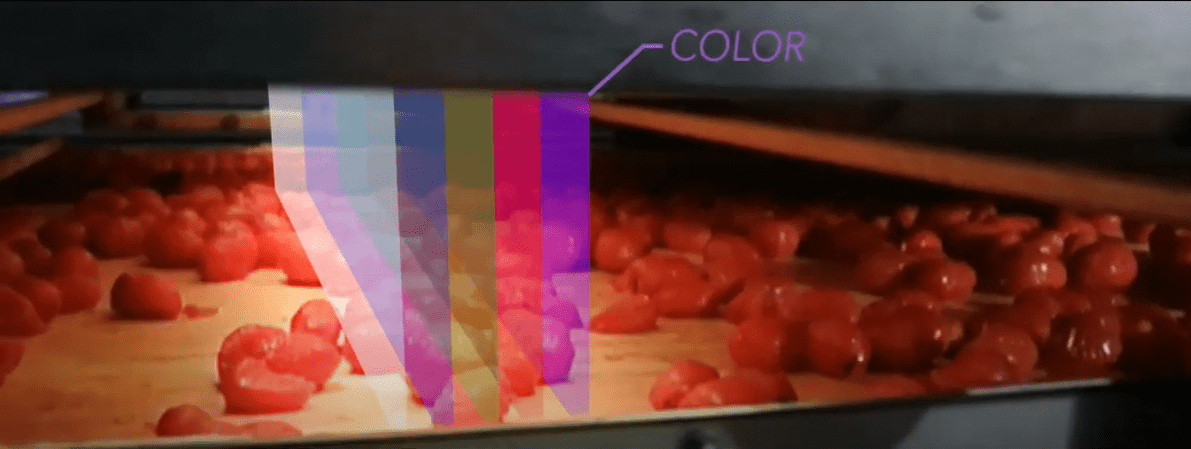
Optical sensor that detects imperfections.
The product is moved by means of a conveyor belt whose function is to stabilize the product so that it does not roll.
In the final part of the conveyor belt there is a drop of about 20cm, during which the products are inspected and eventually ejected: during the few moments of the fall the rejection system with pallets driven by high-speed pneumatic cylinders, mounted below the optical sensors, differentiates the conforming products separating them from the unusable ones and optionally also from those considered second-rate products.
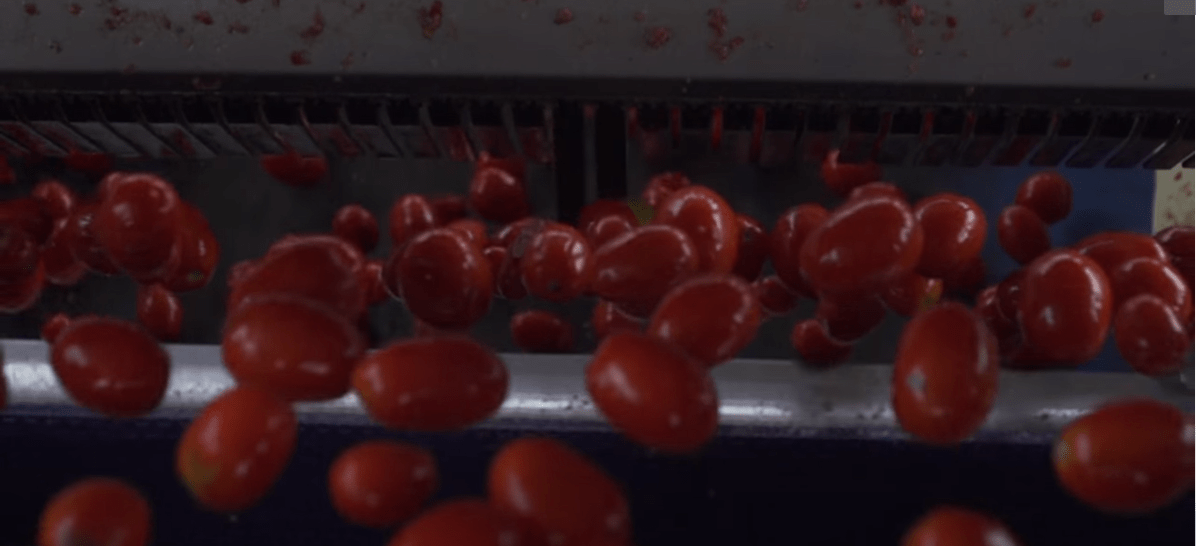
Waste scoop in operations.
One of the key components of this type of sorter is definitely the pneumatic cylinder that drives the blades.
The speed of the machine and the quantity of good product rejected and therefore the quality of the selection are directly determined by the maximum speed and frequency attainable by the pneumatic cylinder.
Given the direct correlation between the performance of the machine and the pneumatic cylinders used, it is clear that over the years higher and higher speeds were required as the continuous improvements in electronics and sensors allowed for even higher performance.
Before long, this technology push made standard solutions obsolete and created the need to develop special cylinders capable of achieving the higher speeds required, up to maximum operating frequencies of more than 20 cycles per second.
The increase in speed also requires a reinforcement capable of resisting the increasingly high stress and harsh environmental conditions typical of the food sector.
On the one hand, it has been necessary to evolve the cylinder in order to reinforce the components most often subjected to dynamic stress, in particular shocks and vibrations, both by selecting the most suitable materials and by adopting specially developed construction solutions.
On the other hand, it was necessary to use materials and designs that would allow for compliance with the strict requirements of food industry standards to avoid possible contamination, but which would also be able to resist, especially as regards seals, both corrosion and wear caused by juices and vegetable residues, but also chemical aggression caused by washing with hot water and acid or basic solutions.
In the design of a pneumatic cylinder for use in a food environment, the aspect of washing is in fact one of the main aspects to pay attention to.
It is essential that surfaces in contact with food must be washed at the end of every work cycle to ensure the hygiene of processed products; this procedure poses a major challenge for machine components, especially when considering the type of seals used.
Gaskets that are typically resistant to hydrolysis caused by hot water and various chemicals are typically delicate and have limited elasticity, making them particularly susceptible to wear and unsuitable for intense mechanical stress due to fouling and high frequencies.
On the contrary, an electric cylinder could provide the solution in terms of frequency from a technical point of view, i.e. cycles per second of operation, but at the same time has much higher production costs than a pneumatic cylinder.
As we will see in the next point, this type of cylinder is subjected to stress and wear for 24 hours every day of the week throughout the vegetable harvesting season which can last several months.
This means that no matter how durable and well-designed a cylinder may be, it requires replacement several times during the different seasons, so as to avoid breakages or machine stoppages that are very costly for companies.
Is there really a solution?
Companies often have great ideas but fail to implement them brilliantly.
This situation creates a ticking time bomb effect because it causes frustration, wastes time and money on research and development, with inadequate solutions that only eventually turn into dead ends.
This process of endless attempts is tiresome, both for the entrepreneur and for internal resources, but above all it can also create very unhappy customers if a subpar solution is put on the market: continuous complaints, damaged image, prolonged assistance with high costs, and returns and refunds are natural consequences of this process that occur daily in companies.
In fact, after having tried with pneumatic and electric cylinders of various kinds, not finding adequate solutions on the market, this leader in the production of sorting machines decided to try an alternative way.
The customer opted for a special cylinder (custom-made), even if at the beginning they were extremely unsure because they thought that not even this solution would deliver the kind of operational safety much sought after in terms of sorting machines.
In fact, a 24/7 operation plus the high corrosiveness of the operating environment made it really difficult to design a cylinder that not only guaranteed the required working levels but also had to be small and corrosion resistant.
Not only did the customer want it to be extremely reliable, with a very high frequency of cycles per second but also to keep costs down, in short, mission impossible, pushing the limits of pneumatics.
In addition, the development of this solution had to be done in the shortest time possible, because the company was under pressure from its customers, who urgently needed reliable machines.
The company and Cy.Pag. have been exchanging emails and phone calls for months, hours and hours spent designing a cylinder that could have all the features described above and that could satisfy our Partner’s customers.After months of work and several test solutions, we arrived at a first solution that was satisfactory for the market.
The cylinder we designed was able to work at very high frequencies, for a long time and to occupy an extremely small space behind the paddle used to reject non-compliant vegetables.
A cylinder at the limit of pneumatics
When you design something that does not exist and therefore, there are no terms of comparison on the market, you need innovative solutions that go far beyond the possibilities of a standard cylinder.
Designing a pneumatic cylinder capable of performing 23 cycles per second, of miniature dimensions, reinforced to resist chemical agents, and as if that were not enough at a competitive price, it was made possible by creating a unique and uncopiable product, capable of making these machines a true technological masterpiece.
When an entrepreneur dreams of building an extremely innovative machine, they go through difficult moments and when they get to the execution of the project, they can finally start the distribution and verify on the market the real interest of their customers.
This company started with a tomato sorting machine with innovative technology specially designed by Cy.Pag. for long life and reliability.
Only innovators can benefit from the so-called “First Mover Advantage”, the advantage of being the first in a new market to introduce a product or service.
On the other hand, however, being the first on the market also exposes the company to risks: a series of field tests are required, which are not always successful.
In this case, the field test had to verify whether the machines designed in this way could resist the attack of the corrosive agents contained in tomato juice, which is highly corrosive, throughout the season.
When developing products using innovative solutions in the presence of various stresses and often conflicting requirements, the decision to carry out field tests is necessary.
Given the imperative need not to interrupt production during the season of harvesting and processing of food products, it was necessary to avoid the costs of machine downtime, but above all the damage to raw materials that risked degradation during the stop.
The aspect of reliability is therefore essential and requires that we do not limit ourselves to theoretical design or laboratory testing: this is why Cy.Pag. made itself available to carry out its own tests and then to collaborate in the execution of tests in the field. Thanks to the positive results obtained during the tests on the harvesting fields, it was possible to release the new machines with the peace of mind given by a proven solution.
In spite of all the problems and constraints to be respected, the launch on the market obtained wide consensus and opened a scenario of wide development: the cylinders resisted to intensive work cycles, corrosive agents and frequent washing throughout the season.
The missing piece to bring the company into development
Can a pneumatic cylinder revolutionize working procedures in the world of agriculture?
The solution of the custom-made pneumatic cylinder brought the company an unprecedented opportunity for entrepreneurial development because, not only was it the first on the market to use this technology, but it had in front of it the concrete possibility of spreading an innovative solution to a widespread problem in the agricultural sector, a bit like how the combine harvester revolutionized the harvesting of wheat, which before then was done by hand.
The strengths of this solution brought a number of advantages:
-
A much lower production cost than an electric cylinder, resulting in the ability to replace cylinders between seasons with less economic impact. The company was thus able to decrease the production and maintenance costs of the machines;
-
The high operating speed allows the machine to do its job faster and with less good product discarded;
-
The higher mechanical and chemical resistance reduces the frequency of maintenance interventions during the harvesting season.
In particular, resistance and reliability are fundamental aspects for those who work in this field, because machine downtime generates enormous costs: production downtime does not only cause the blockage of machines and manpower, but also the very rapid deterioration of vegetables, which risk rotting in a very short time, thus having to throw away tons of product.
A Partnership to create a competitive advantage
Surely this, or rather these projects have created a solid collaboration with Cy.Pag., which has been going on for more than 20 years.
The cylinders that have been designed have been patented for a long time, they are therefore a proprietary solution that cannot be copied by competitors, thus generating a long-lasting competitive advantage.
All this has been possible because the company has outsourced the task of designing a very particular component that requires in-depth technical knowledge, relying on our design studio, which has over 25 years of experience in the sector and has carried out more than 5,000 special projects.
This collaboration was possible thanks to the continuous communication and assistance of the highly qualified technical staff, which allowed the company to have a prompt response to the problems encountered along the way and to be more comfortable knowing they had a strong and technically prepared partner.
Since the beginning of the collaboration with this company, Cy.Pag. has been carrying on a continuous improvement of the special cylinder with more and more advanced solutions, now at the 10th version, a bit like Apple does with its products, even more mechanically robust and with a better resistance to corrosion than the previous versions.
In fact, some measures have been applied to strengthen the cylinder structure and to work at higher and higher frequencies, in order to better meet the needs of the manufacturer, which allows the cylinder to have a longer life.
Cy.Pag. has developed a free evaluation service for companies that want to compare the competitive advantages that a tailor-made cylinder can bring to their machines, such as the Monda Bench, the optical or sensor sorter, the foreign body sorting belt.
The consultancy is divided into two phases:
Contact by Telephone for pre-assessment with one of our specialized technicians;
Pre-Analysis of the technical information provided by the customer with specification of the benefits of designing a custom-made cylinder.
After developing thousands of custom cylinders, we have developed an extremely effective protocol to not waste the companies’ time, but to get straight to the essential information.
Call one of our Technical Tutors now to find out how to gain a competitive advantage in your market sector.
From ’98 to January 2021, we have sold nearly 270,000 special cylinders for this application.