When we talk about blast furnaces, specifically Ilva one, located in Taranto (the largest steel mill in Europe)the first things that might come to mind are rather air pollution and workers’ safety issues; this is due to the Italian daily news which has always given prominence only to negative news.
We all remember how, in 2019, the Italian judiciary system obliged Ilva to isolate blast furnace number 2 for safety reasons.
In order to proceed with safety measures, the blast furnace must necessarily be turned off, so that the machines can be installed.
Why does the safety of the blast furnace cause such a weird feeling?
The answer is straightforward: such complex a system cannot be turned off; it is not enough to press the “OFF” button, but it takes about 30 working days and 34 different operations in an exact sequence to complete a very long and scrupulous safety shutdown procedure.
These operations are necessary because the sudden and hasty shutdown of the blast furnace can jeopardize its re-ignition, while if done correctly it does not cause any kind of problem.
These are the reasons that among others (for example pollution)generated scoops and about which many newspapers and TV channels have spoken.
The truth, however, is that the progress and well-being, in Italy as in the whole world, are closely linked to the production of metals, which are the raw material for the production of most products, namely cars and industrial machines.
There are also smaller blast furnaces than Ilva, kept under strict control from polluting emissions and safety, which do not represent a danger, but a great opportunity for our country to grow, improve and invest in technology.
Basically, the blast furnace is a very complex structure that requires extreme safety measures as it works at temperatures that can reach 2000°C and which expose workers to extreme risks.
Table of contents
Blast furnace: industrial challenges
Over the years we have cooperated with manufacturers of blast furnaces and ancillary machines to ensure the correct functioning of the system, but above all to increase the safety of workers and the working environment.
The biggest challenge is to use high-temperature-resistant materials and a cylinder structure that avoids problems during the processing and operations of opening and closing the loading door of the blast furnace (operated by a pneumatic cylinder), which according to the dimensions can reach up to 4 quintals in weight.
The reliability of the components has never been as important as in the case in question, in fact, the steel sector, as well as metallurgy, as previously mentioned has an average hourly cost of downtime that exceeds $500,000: you understand how essential it is that everything goes as planned and there are no hitches? The downtime costs and losses are too high.
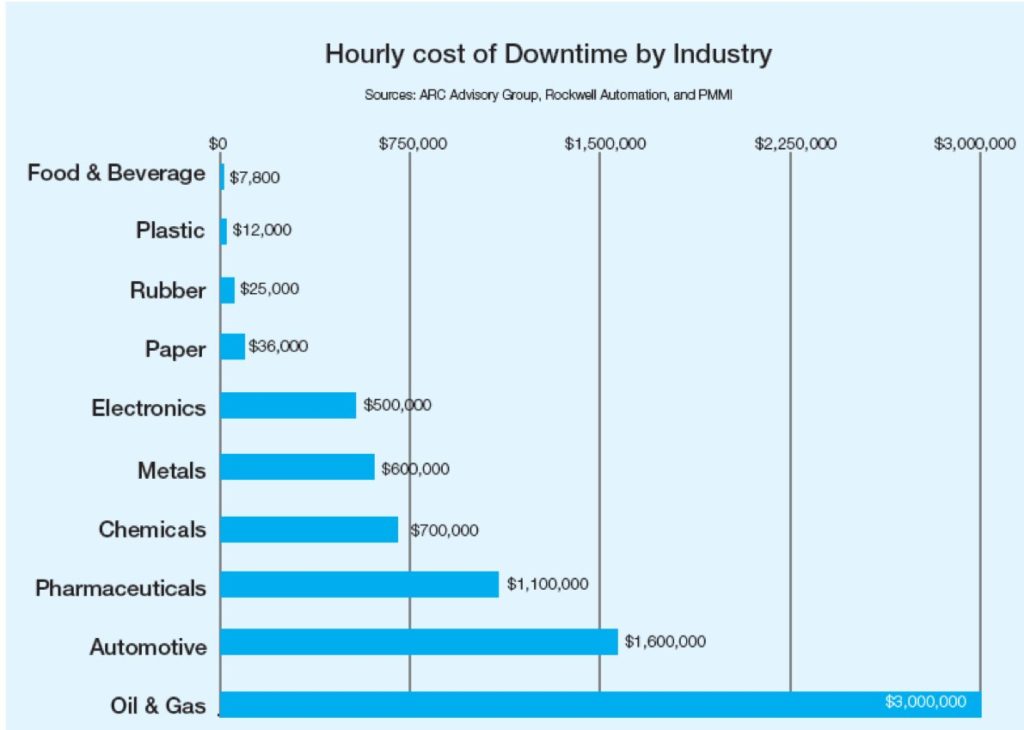
Furthermore, if the cylinder for opening and closing the loading door is damaged or broken, (in the specific case we are talking about a medium-sized blast furnace), it takes about 4 days to cool the furnace, 1 day of maintenance for the replacement of the piece and another 3 days to restart the oven.
This shows how important it is to plan maintenance correctly and to dispose of extremely reliable components (including pneumatic ones).
Bearing in mind the costs caused by a shutdown highlights the importance of maintenance and safety due to the reliability of machines and individual components. The question should therefore not be underestimated: now let’s see the peculiarities of pneumatic components for the metallurgical industry.
High reliability and resistance pneumatics
Pneumatic applications for the metallurgical industry must take into account the characteristics of the working environment of this sector, and therefore be designed accordingly.
Often the solutions that are designed are tailor-made for the particular needs of different customers, with an eye to extreme temperatures, high pressures and loads, shocks and aggressive fluids.
Another special attention goes to the impurities of the molten and hot metal, which might splash and can be placed on the rod.
If this happens they can melt and create a hump which during the stroke would destroy the gasket, thus compromising the functionality of the pneumatic cylinder.
These are some characteristics that cannot be ignored during the design phase and that lead to the choice of special and very resistant materials in order to guarantee longer life and greater reliability to the cylinder.
The harsh conditions under which a well-built pneumatic cylinder does not bend to
We have previously listed the problems that a pneumatic cylinder could face in this work environment, now let’s see how it must be built to be able to last longer, without damaging the company’s economy.
To solve the problem of hot residues and slags that can compromise the surface quality of the rod, Cy.Pag. has adopted a sheath, protective cap, with a strategically positioned air filter to avoid damaging the cylinder.
A metal blades-equipped rod scraper is also applied, which has the function of removing any impurities and cleaning the rod from dust or hard encrustations: this guarantees a longer life and durability for the cylinder.
Another problem is the extreme temperatures that are reached, which can be harmful especially on the seals: the rubber in fact “loosens”, cooks or becomes glass.
Viton, used by Cy.Pag., Contains fluorine which allows maintaining the elastic function of the gasket. This, combined with PTFE or metal shielding elements, attenuates the effects of high temperatures, thus allowing the use of the cylinders even with temperature peaks up to over 200°C.
The actual application is not a laboratory test
One of our customers maintains a furnace for processing metals at high temperatures operating, where the pneumatic cylinder (as previously mentioned) is used to open and close a door of 4 quintals to allow the trolley to let the metals enter and exit the furnace.
A 320mm diameter cylinder and 1450mm stroke has been specifically designed for this application, with an extended rod and Viton seals.
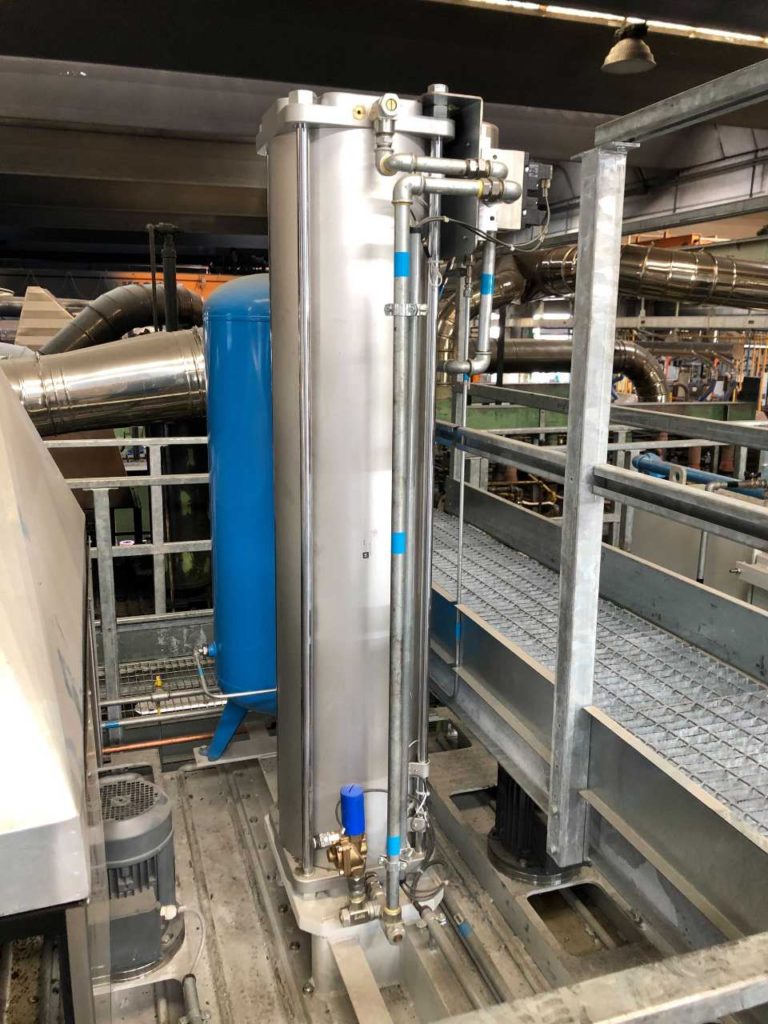
After various tests and minor improvements, such as the addition of a gasket protection screen, the cylinder was finally assembled and went into operation.
Our cylinders for the metallurgical industry, compared to those of the competition, are heavier (which is a plus for these applications), which makes them more reliable in the medium and long term; to better withstand heavy work and despite everything, they are also able to maintain a more competitive price thanks to a mix of price-saving measures from our technical department.
If you have a company that works in this sector, or if you take care of the management or maintenance of this type of system, do not hesitate to contact us to know more about how we can improve your life by simplifying and reducing maintenance operations, with a more reliable, custom-made and specific cylinder saving you money over time.
Call us at +39 0342 60 50 11 or write us an email at info@cypag.com to request a free consultation.