With a 61% increase in 16 years, the world’s consumption of plastic bottles has risen from 300 billions in 2004 to 583.3 billions in 2020, putting a strain on the bottling industry, according to Euromonitor, an international research institute.
We are active in 10 industrial sectors (Food, Pharma, Wood, Marble & Stone, Beauty, Bus and Train Doors, etc.), and bottling is undoubtedly one of those with the highest growth rates.
This situation has put a lot of pressure on the sector, which in order to deal with the huge increase, needs tools and resources to strengthen its production capacity.
This is the case of one of our customers, who is one of the main players on the Italian market and produces machines and systems for the so-called “Bottling” process, i.e. the production of bottles or more generally bottle-sized packaging.
Table of contents
When is a pneumatic cylinder used?
Let us start with a premise: the “competition” in this sector pits pneumatic cylinders against electric cylinders.
In this case we are talking about the actuators for the sides. The bottles slide on very long guides and many actuators are required to automate the bottle size changeover almost instantaneously.
There are two key features that determine the choice of a pneumatic cylinder rather than an electric one, and they are price and the flexibility that the machine or system will need to have.
If we talk about price then the pneumatic cylinder is the best choice, a cylinder for this type of system can cost even 10 times less than an electric actuator; so, if the variable of flexibility can be neglected there are no doubts about which is the choice.
When the machine needs a certain degree of flexibility, which we will get into shortly, then the electric cylinder is undoubtedly the choice that is made at the time of purchase and in the design phase.
Why is this last point so crucial?
The answer is quite simple, but it requires a brief description of how the system works.
Main differences between Pneumatic and Electric
The cylinders move the guides that support the plastic bottles in the blowing and filling system. As you well know (just look at the supermarket shelves), there are thousands of different bottle formats. In recent years, in fact, with the increasing valorisation of packaging, there has been an explosion of the strangest formats with extremely variable sizes.
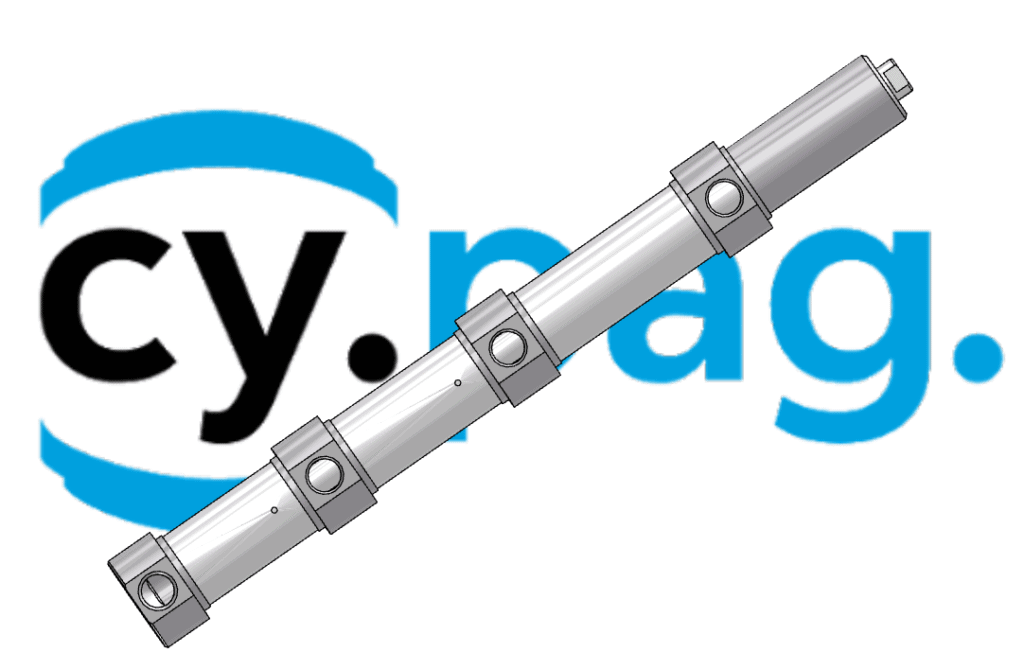
“Tandem” pneumatic cylinder can stop in 3 different positions (thanks to a mechanical system) and therefore manage 3 different production lines for bottling plants:
Retracted rod
Extended rod, first intermediate step
Extended rod, second final step
On the contrary, the electric cylinder can reach any point of the stroke (with an accuracy of even a tenth of a millimetre) and stop.
Result: the production line becomes universal without requiring any readjustments.
The choice guided by the customer's needs
What determines the choice of one product over another? Simply the need of the end customer.
When the need is to have a semi-rigid system, which can manage up to 3 product lines, then the pneumatic choice is obvious.
Hundreds of cylinders are installed on a system, buying them at 1/10 of the electric competitor makes all the difference in the world, especially in terms of market competitiveness.
If, on the other hand, the need is to have a flexible line, then the natural choice would be the electric cylinder, which, despite being more expensive, allows for multiple combinations and positions to manage different products.
In this case (for a flexible system), in order to be able to manage more than 3 product lines with the pneumatic cylinders, it is mandatory to change the cylinders each time there is the need to make a bottle with sizes different from the 3 foreseen by the cylinders installed.
It goes without saying that in this case, despite having the cylinders at a much lower price, it will take a while to be able to change the cylinders of the entire line.
Final considerations
It is now clear that the choice of one solution over the other is driven by the customer’s need to have a semi-rigid and much cheaper plant or a flexible but much more expensive production line.
There are not many other evaluations to make when choosing a cylinder.
Cy.Pag., as supplier of pneumatic cylinders to the customer in question, has been cooperating for years with excellent results in terms of final customer satisfaction, obviously referring to the supply of cylinders for semi-rigid systems as described above.
To have a detailed view of the possibilities that Cy.Pag. offers in this sector, contact us at +39 0342 60 50 11 and ask for the free advice of one of our pneumatic consultants, or write us an e-mail to info@cypag.com with all the details that you are interested in.