Il mercato delle macchine tessili industriali è in continua e rapida evoluzione, con innovazioni che portano da piccoli a grandi benefici a chi produce in questo dell’Industria Tessile Tecnologia.
I costruttori di macchine non possono permettersi di rimanere indietro e rischiare di soccombere alla concorrenza: innovare è la chiave della sopravvivenza.
Facendo una panoramica dei numeri di vendita dell’ultimo periodo l’indice degli ordini per le macchine tessili elaborato da ACIMIT, l’associazione dei costruttori italiani, ci indica che nel trimestre gennaio-marzo 2021 è risultato in crescita del 66% rispetto al medesimo periodo del 2020.
Come riportato nel grafico che segue, dopo anni di crescita costante dal 2012 al 2017, il mercato aveva registrato ottimi numeri, trend poi invertito dal 2018 in poi.
In questa condizione di difficoltà, il nostro cliente ha saputo mantenere preziose quote di mercato grazie anche al vantaggio competitivo dato dalla scelta dei componenti pneumatici.
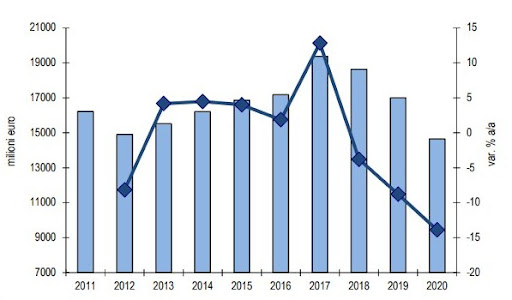
Tale risultato è dipeso dal buon andamento della raccolta ordini sia all’estero che in Italia.
Tornando al 2021 sui mercati esteri l’incremento è stato del 68%, sul mercato italiano la crescita degli ordini è stata più contenuta, ma comunque interessante (+54% rispetto al primo trimestre 2020).
Questa crescita è stata trainata dalla forte ripresa dei mercati post prima ondata di Covid-19, ci sono però le basi per presupporre che il mercato abbia già in parte assorbito lo shock della pandemia e sia pronto a viaggiare a livelli pre 2020, se non superiori.
Anche per te, imprenditore e costruttore di macchinari tessili, è venuto il momento di continuare il processo innovativo e cavalcare quest’onda di ripresa per non rimanere in coda ai tuoi competitor.
Tabella dei Contenuti
Le problematiche produttive delle macchine tessili industriali
Oggi vi parlerò di un’azienda che produce macchine per la lavorazione (texturizzazione) del nylon, che vengono utilizzate per la produzione di calze da donna.
Queste macchine vengono messe in fila per lavorare un filo alla volta, ogni singolo rocchetto viene posizionato sul mandrino e fatto girare a velocità molto elevate, fino a 18.000 giri/minuto.
Il processo è molto importante per il risultato finale del filato, ci deve infatti essere una tensione costante che permetta di eseguire la lavorazione senza rovinare il tessuto.
Nel caso in cui la tensione dovesse cedere, o calare di molto le macchine si fermano e sopraggiunge il blocco di produzione. Invece, se la tensione è troppo elevata, il filo rischia di rovinarsi o addirittura rompersi.
È quindi chiaro che vengono eseguiti dei monitoraggi costanti e molto precisi sulla tensione.
L’innovazione è anche pneumatica
Per costruire un sistema rotativo ad alte velocità, con un sistema pneumatico che permettesse il cambio del rocchetto di nylon in modo completamente automatizzato, senza interruzioni, ci sono volute molte ore di lavoro e un contatto costante tra Cy.Pag. e l’azienda costruttrice di macchine.
Il prodotto finale doveva essere qualcosa di nuovo, rivoluzionario, diverso da tutto ciò che era standard.
Come primo step si sono tenuti dei meeting, scambi di email per la tracciabilità della commessa e visite sul campo dei nostri ingegneri per capire il funzionamento della macchina e le esigenze del cliente.
Una volta chiarite, Cy.Pag. ha iniziato la progettazione di un cilindro totalmente nuovo, che ora andremo a scoprire nei dettagli.
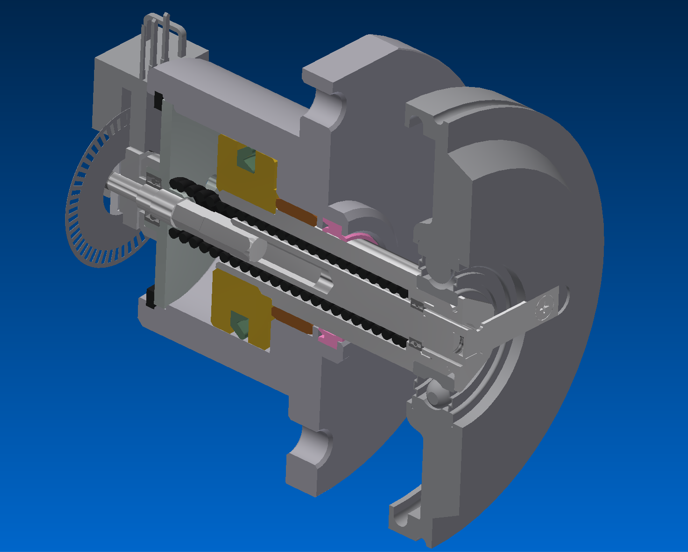
Il primo cilindro svolge la funzione di mandrino con sistema di sgancio rapido del rocchetto esausto. Venne sviluppato più di venti anni fa ed è stato utilizzato ininterrottamente fino ad oggi per produrre centinaia di macchine texturizzatrici.
Come si può intuire la velocità di cambio del rocchetto gioca un ruolo fondamentale, questa consente di mantenere la produzione continua e in questo senso la velocità del cilindro pneumatico rispetto agli altri tipi di attuatori gioca un ruolo importante.
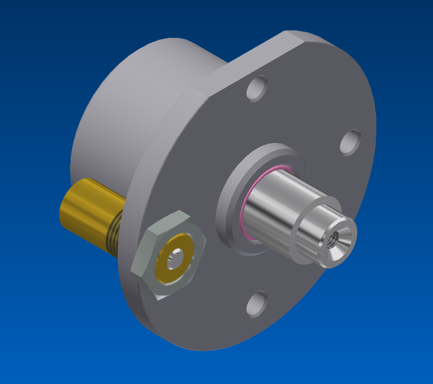
Ci sono poi altri aspetti del sistema molto importanti da tenere in considerazione.
Il mandrino deve essere estremamente compatto in relazione alla dimensione assiale. Questo permette di ridurre le dimensioni della macchina con conseguenti vantaggi economici.
Un altro aspetto molto importante che contraddistingue questo prodotto di eccellenza è la grande precisione della guida del mandrino.
Infatti la texturizzatrice, che viene prodotta da un’azienda leader a livello mondiale, è caratterizzata da elevatissime velocità di funzionamento che si riflettono nello svolgimento dei rocchetti ad oltre 18.000 giri/min.
Il mandrino pneumatico deve quindi girare a tali velocità senza introdurre oscillazioni dovute ad eccentricità, sostenendo le elevate vibrazioni create dalle irregolarità di forma del rocchetto di filo. É quindi stato studiato per garantire il massimo allineamento possibile nonostante le dimensioni compatte.
Il successo del progetto ha garantito, pur con continue evoluzioni negli anni, un rapporto di lavoro più che ventennale.
Un’evoluzione di prodotto continua
Con il passare del tempo e i continui test sul campo del nuovo cilindro sono nate nuove esigenze.
L’evoluzione del mercato e delle tecnologie delle macchine per la texturizzazione ha portato alla necessità di aumentare il controllo sulle velocità di svolgimento e riavvolgimento dei rocchetti.
La regolazione delle velocità e delle tensioni rende possibile aumentare i ritmi di produzione, allo stesso tempo è anche possibile ridurre i fermi dovuti a rottura del filo e migliorare il controllo sull’avvolgimento dei fili sui rocchetti.
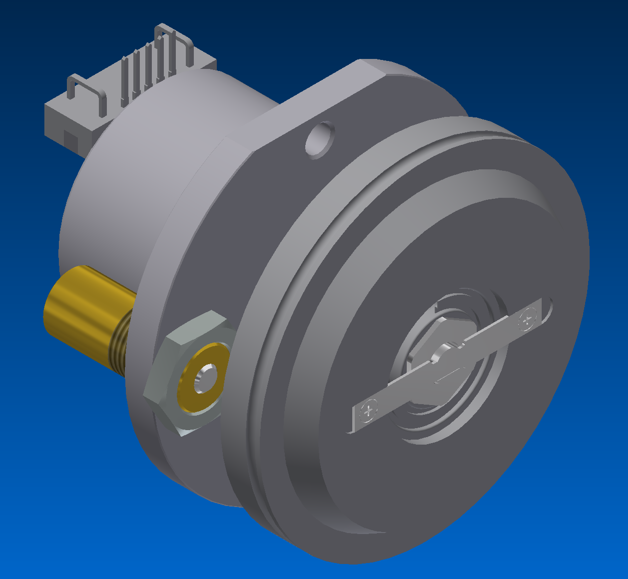
Questa necessità si è tramutata in una richiesta da parte del cliente di avere un albero nella parte opposta alla flangia rotante che trasmettesse la rotazione della flangia stessa, e quindi del rocchetto, così da poter consentire il montaggio di un encoder che consentisse di leggere in tempo reale la posizione angolare del rocchetto.
Il tutto avrebbe dovuto essere abbinato ad una ulteriore riduzione della lunghezza totale della contropunta al fine di poter alloggiare l’encoder senza incrementare le dimensioni delle macchine.
L’obiettivo è stato raggiunto inserendo due alberi coassiali allo stelo del cilindro che consentono la trasmissione del moto rotativo pur permettendo il movimento di estensione e ritorno dello stelo.
Il tutto è stato realizzato senza creare eccentricità degne di nota che destabilizzassero la contropunta e senza ridurre la resistenza alle oscillazioni causate dal rocchetto.
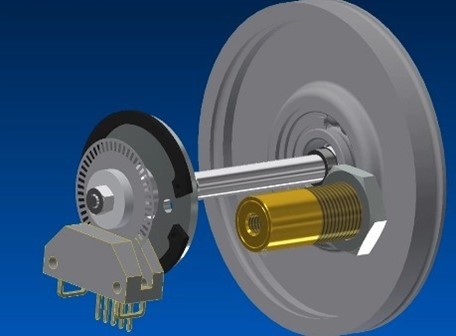
Le elevate sollecitazioni sugli elementi di congiunzione miniaturizzati hanno imposto di utilizzare elementi in acciaio temprato ad alta resistenza per garantire la vita utile minima richiesta.
I test effettuati dal cliente hanno confermato la piena soddisfazione delle richieste.
Ottimizzazione per creare valore
L’ottimizzazione nel tempo dei nostri progetti custom è uno dei punti di forza Cy.Pag., che non solo crea valore per il cliente in un dato momento storico, ma apporta delle modifiche migliorative che permettono di mantenere il vantaggio competitivo a lungo nel tempo.
Cerchiamo infatti di stabilire un legame forte e duraturo, non lasciando mai soli i nostri clienti e aiutandoli a cercare le soluzioni più efficaci.
Il case study che ho appena descritto ha permesso, e permette tutt’ora, all’azienda costruttrice di macchine per il settore tessile di avere un prodotto finale di altissima qualità, grazie anche ai nostri cilindri creati su misura.
I vantaggi principali che questa soluzione ha apportato sono: affidabilità e robustezza (che sono delle costanti che ricerchiamo sempre nei nostri progetti creati su misura), velocità di esecuzione delle lavorazioni e controllo dell’applicazione.
Nel nostro Blog trovi molti Case Study in diversi settori industriali, dai un’occhiata di come le nostre storie di successo hanno aiutato tanti imprenditori a crearsi un mercato ed un vantaggio competitivo rispetto alla concorrenza.
Richiedi ora una consulenza gratuita per la tua azienda chiamando il numero +39 0342 60 50 11 oppure scrivendoci una mail con le tue esigenze a info@cypag.com, saremo a tua completa disposizione per un’analisi tecnica.