Molto spesso si parla di contaminazione dei cibi; giornali e telegiornali girano il coltello nella piaga contro le aziende che mettono a rischio la sicurezza dei consumatori.
Avete mai sentito parlare di contaminazione dei cosmetici?
Già, i cosmetici sono a contatto con la pelle, con le mucose e possono veicolare infezioni e rischi microbiologici altrettanto gravi.
I cosmetici infatti hanno una data di scadenza, esattamente come i cibi, con una sigla riportata sulla confezione di 3M, 6M, 12M, 18M, 24M o 36M, che corrispondono ai mesi di scadenza.
Il pericolo più grande si riscontra durante il confezionamento, perché eventuali residui incastrati nelle macchine dosatrici possono contenere agenti patogeni, come lo Staphylococcus (acne e desquamazione della pelle), il Bacillus Cereus (gravi infezioni agli occhi) o la Candida (eruzioni cutanee e dermatiti).
Lo sanno benissimo i produttori di macchine ed anche i manutentori, che devono fare molta attenzione alla manutenzione dell’impianto e pulire le macchine frequentemente per evitare che residui indesiderati entrino in contatto con il prodotto causando infezioni ai consumatori (es. Shampoo, Creme per il viso, etc.).
In questo settore, come quello del Food, la pulizia degli ambienti e dei cilindri stessi è essenziale per restare in commercio ed evitare cause legali dei consumatori.
Facciamo un esempio pratico, accaduto ad un nostro cliente nel settore alimentare: tempo fa, un’azienda di produzione di prosciutti era in procinto di procedere con una operazione di routine, ovvero la disossatura dei prosciutti.
Questo è un processo altamente meccanizzato, che si effettua quando la carne non è ancora stagionata.
Per fare questa operazione si decongelano lotti di prosciutti da 1.500/2.000 pezzi, che una volta preparati devono essere lavorati entro poche ora, altrimenti rischiano di rovinarsi, ma soprattutto non possono essere di nuovo messi in congelatore in caso di ritardi.
Prima di iniziare la lavorazione, i responsabili si accorsero che le macchine non funzionavano correttamente e questo avrebbe potuto bloccare tutto il processo. Rimanendo fuori dai congelatori, il lotto di carne poteva contaminarsi, rendendolo così da buttare.
Ecco perché i dirigenti furono obbligati a destinare ogni singolo dipendente (compresi i dirigenti stessi) a macellare a mano i prosciutti per contenere il danno, che sarebbe aumentato a dismisura con il passare del tempo.
Di certo nel settore del Beauty non abbiamo materiali deperibili così rapidamente come la carne appunto, ma i fermi macchina (nei peggiori dei casi) o comunque i ritardi per la manutenzione, hanno un impatto negativo sia sulla produttività che a livello economico.
Nel caso studio, parleremo dell’analisi che è stata fatta sugli impianti di riempimento, per poter progettare e poi produrre dei Cilindri Pneumatici su Misura che consentissero di ridurre drasticamente i tempi di manutenzione e pulizia.
Tabella dei Contenuti
Come funzionano i Cilindri Pneumatici dosatori del settore Beauty?
La funzione che deve svolgere un Cilindro Pneumatico su questo tipo di impianto è tanto semplice quanto delicata.
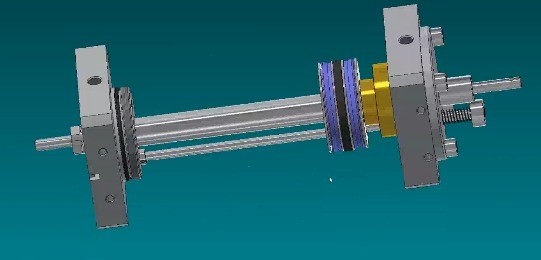
Un manubrio regola la corsa del cilindro e permette di scegliere la quantità di prodotto che deve essere pompata dalla macchina per riempire il contenitore al punto giusto.
Questa è la prima operazione, da fare prima di lanciare l’impianto alla produzione.
Dopodiché viene avviato l’impianto, con l’azionamento dell’aria compressa il cilindro entra in funzione e ad ogni ciclo riempie i contenitori della linea di produzione.
Per garantire la completa sterilità dell’ambiente di lavoro, questi cilindri richiedono una costante manutenzione: pulizia e cambio delle guarnizioni, per evitare il deposito di residui contaminanti.
Il cilindro standard richiede tempi relativamente lunghi per essere smontato dal suo alloggiamento, poi aperto (svitando i tiranti), ed infine pulito accuratamente; dopodiché si ripete tutto il processo al contrario per rimontare tutto.
Una macchina con 8 cilindri richiede un grosso investimento in termini di tempo per la manutenzione, tanto da rendere estremamente vantaggioso investire sulle ottimizzazioni del processo di manutenzione.
Vediamo quali sono stati i passaggi salienti per la progettazione e produzione di questo tipo di Cilindri.
Le sfide: abbattere tempi e costi per aumentare la produttività
Nel Case Study sul Food, che ti invito a leggere cliccando qui, spesso si riscontrava un malfunzionamento dell’impianto, legato ad un cilindro che non era in grado di raggiungere le prestazioni richieste da quell’applicazione (prima di portare un miglioramento con la nostra soluzione).
In questo caso la storia è andata in modo diverso: infatti, non erano presenti grossi difetti nell’applicazione, che durante l’operatività funzionava perfettamente, ma quella tecnologia rendeva davvero difficile la manutenzione e la pulizia dell’impianto.
Era arrivato il momento di innovare e trovare un modo per aumentare la produttività e rendere la vita più facile ai manutentori.
Qual era il problema più grande che le vecchie macchine presentavano?
Come abbiamo detto, in questo settore veniva eseguita una manutenzione ordinaria molto frequente.
Bisognava smontare gran parte della macchina per raggiungere le viti del cilindro (posizionate sul retro) e sostituire le guarnizioni o fare pulizia.
Questo tipo di operazione ricorda molto il lavoro dei meccanici, quando devono smontare la pompa dell’acqua che è in una posizione poco accessibile, e quindi sono costretti a tirare giù tutto il motore per poter completare il lavoro.
L’operazione richiedeva al manutentore circa 10/15 minuti a cilindro, il che non è un tempo estremamente alto, ma se consideriamo di doverla eseguire su 8 cilindri per macchina, su 10 macchine, allora il tempo diventa ad essere un fattore da tenere in considerazione.
Come già detto, non è una questione di funzionalità della macchina, ma ottimizzare questo processo avrebbe fatto risparmiare tutti i giorni ore di lavoro, che potevano essere utilizzate per fare altre mansioni più produttive: abbassando così i costi per la manutenzione della macchina stessa.
La manutenzione va fatta bene, perché i sedimenti di prodotto, oltre a costituire un rischio di contaminazione, possono corrodere il cilindro, causando gravi danni e riducendo la vita del cilindro.
Come abbiamo visto nel caso del Food, i danni sono davvero ingenti e lo stesso principio vale per chi produce cosmetici.
Qualsiasi parte del cilindro che possa favorire la sedimentazione del materiale diventa un’area da manutenere frequentemente.
Ad esempio i tiranti del cilindro favoriscono il deposito di materiale e richiedono una manutenzione maggiore proprio per l’attenzione che si deve avere per eliminare tutti i sedimenti di prodotto/agenti corrosivi.
Un nuovo cilindro, più semplice da gestire
Quando il nostro ufficio tecnico ha iniziato la progettazione del nuovo cilindro aveva chiaro fin da subito che sarebbe stato pensato per:
Semplificare la vita dei manutentori;
Rimuovere ogni parte che favorisse il deposito di prodotto/agenti chimici sul cilindro.
Come si poteva rendere più semplice la manutenzione, senza compromettere la funzionalità del cilindro?
La soluzione è tanto semplice, quanto efficace.
Abbiamo scomposto la testata del cilindro in 2 componenti: quello centrale è rimovibile come una sorta di tappo svitando 4 viti facilmente accessibili, e permette di pulire rapidamente e sostituire le guarnizioni, senza perdere un minuto di tempo.
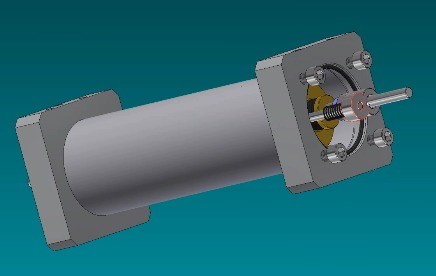
Quindi, andiamo a paragonare i 2 processi di manutenzione:
Con il vecchio sistema bisognava smontare la macchina da sotto in una posizione scomoda, rimuovere 8 viti in diverse posizioni, estrarre il cilindro, aprirlo ed effettuare pulizia e sostituzione delle guarnizioni. Terminata la lavorazione eseguire tutti i passaggi a ritroso per rimontare tutto. Ripetere per ogni cilindro. Un lavoro eccessivo come lo smontaggio del motore per cambiare la pompa dell’acqua!
Ora, con il nuovo cilindro, basta togliere 4 viti, pulire e sostituire le guarnizioni, e il gioco è fatto.
Questa strada ha permesso di ridurre i tempi di manutenzione ad un decimo del tempo precedente e di poterne aumentare la frequenza, migliorando così il rendimento della macchina e riducendo il rischio di contaminazione.
Se prima si perdevano 20 minuti per queste operazioni, ora in 2/3 minuti viene portato tutto a termine.
Come abbiamo detto in precedenza, questa operazione viene fatta non su una, ma su più macchine: moltiplicando il tempo risparmiato per 10 macchine abbiamo un risparmio totale di 2/3 ore ad ogni manutenzione.
Facendo i conti, non abbiamo solo il risparmio di tempo, ma possiamo anche intervenire molto più rapidamente in caso di blocco macchina, azzerando quasi completamente i ritardi di produzione.
In aggiunta, per quanto riguarda il design del cilindro e la sua funzionalità, il nostro ufficio tecnico ha deciso di rimuovere i tiranti, che favoriscono notevolmente l’accumulo di materiale e dunque la corrosione del cilindro stesso.
Questa scelta ci porta ad avere, come si vede dall’immagine, un cilindro dal design estremamente minimal, ma con caratteristiche che lo rendono unico; nonché la miglior scelta per questo tipo di applicazione.
L’assenza di tiranti migliora la pulizia, perché questo punto delicato in cui si concentrano residui contaminanti, non esiste più e quindi non necessita di pulizie talvolta complicate, quando il residuo resta attaccato nelle insenature.
La conquista del mercato
Le strategie di progettazione che hanno portato al risultato finale di un cilindro senza tiranti e con un sistema per la manutenzione rapida, sono state molto apprezzate dal nostro cliente, che ha guadagnato un vantaggio competitivo non indifferente nei confronti dei suoi concorrenti, ancora legati ad un sistema obsoleto.
Non solo, la soluzione è stata mutuata in altri settori (con caratteristiche simili), andando a semplificare i processi di manutenzione e pulizia, e facendo così risparmiare tempo ai manutentori e migliaia di €uro agli imprenditori.
Ci si aspetterebbe che il prezzo del nostro cilindro sia più alto dati gli accorgimenti presi per migliorare la situazione del nostro cliente, invece no, siamo riusciti a mantenere un prezzo equivalente, ma con dei benefici nettamente superiori.
Qualsiasi imprenditore sa che vale la pena di spendere qualche spicciolo in più per risparmiare migliaia di euro, con un enorme ritorno sull’investimento.
La partnership che si è creata con il cliente dura ormai da anni, con continue innovazioni di prodotto e soddisfazione dei suoi clienti finali.
In Cy.Pag. infatti non pensiamo solo ai nostri clienti, ma anche ai bisogni ed alle esigenze dei clienti dei nostri clienti; questa è una delle nostre forze, che ci rende leader nella produzione e commercializzazione di cilindri pneumatici su misura e fa sì che ogni anno i resi non superino lo 0,46%, a testimonianza di quanto siano affidabili i nostri prodotti.
Per avere un vantaggio competitivo quasi sleale, che ti faccia emergere tra i tuoi concorrenti, contatta un consulente pneumatico al +39 0342 60 50 11 oppure scrivi a info@cypag.com per ottenere una consulenza gratuita, durante la quale analizzeremo la tua situazione specifica e ti guideremo nella scelta del cilindro più adatto a te.