Quando si parla di Altoforni, viene subito alla mente l’Ilva di Taranto (l’acciaieria più grande d’Europa), inquinamento atmosferico e sicurezza dei lavoratori, perché le cronache italiane hanno da sempre dato risalto unicamente alle notizie negative.
Ricordiamo tutti come, nel 2019, la magistratura obbligò l’Ilva alla messa in sicurezza in particolare dell’altoforno numero 2.
Per poter procedere alla messa in sicurezza l’altoforno va necessariamente spento, così che le macchine possano essere installate.
Perché la messa in sicurezza dell’altoforno fa così scalpore?
La risposta è molto semplice, è un sistema talmente complesso che per spegnerlo non basta premere il pulsante “OFF”, ma servono circa 30 giorni di lavoro e 34 diverse operazioni in sequenza per completare una procedura di spegnimento in sicurezza molto lunga e scrupolosa.
Queste operazioni sono necessarie perché lo spegnimento repentino e frettoloso dell’altoforno può pregiudicarne la riaccensione, mentre se eseguita correttamente non provoca nessun tipo di problema.
Sono questi i motivi che tra gli altri (ad esempio l’inquinamento) hanno fatto molto scalpore e dei quali hanno parlato molte testate giornalistiche e canali TV.
La verità, però, è che il progresso ed il benessere non solo dell’Italia, ma del mondo intero, sono strettamente legati alla produzione dei metalli, che sono la materia prima per la produzione della maggior parte dei prodotti, delle auto e delle macchine industriali.
Esistono anche altoforni di dimensioni più ridotte rispetto all’Ilva, tenuti sotto stretto controllo per le emissioni inquinanti e la sicurezza, che non rappresentano un pericolo, ma una grande opportunità per il nostro paese di crescere, migliorare ed investire in tecnologia.
Di base l’altoforno è una struttura molto complessa che necessita di misure di sicurezza estreme, infatti lavora a temperature che possono raggiungere i 2000°C e che espongono i lavoratori a rischi estremi.
Tabella dei Contenuti
Altoforno: le sfide industriali
Negli anni abbiamo collaborato con produttori di altoforni e macchine accessorie per garantire il corretto funzionamento del sistema, ma soprattutto per aumentare la sicurezza dei lavoratori e dell’ambiente di lavoro.
La sfida più grande è quella di utilizzare materiali resistenti alle alte temperature e una struttura del cilindro che eviti problemi durante le lavorazioni e le operazioni di apertura e chiusura della porta di carico dell’altoforno (azionata da un cilindro pneumatico), che in base alle dimensioni può raggiungere anche i 4 quintali di peso.
L’affidabilità dei componenti non è mai stata così importante come nel caso in questione, infatti il settore siderurgico, nonché della metallurgia, ha un costo orario di fermo macchine medio che supera i 500.000$: capisci quanto è fondamentale che tutto vada come programmato e non ci siano intoppi? I costi di fermo e le perdite sono troppo elevate.
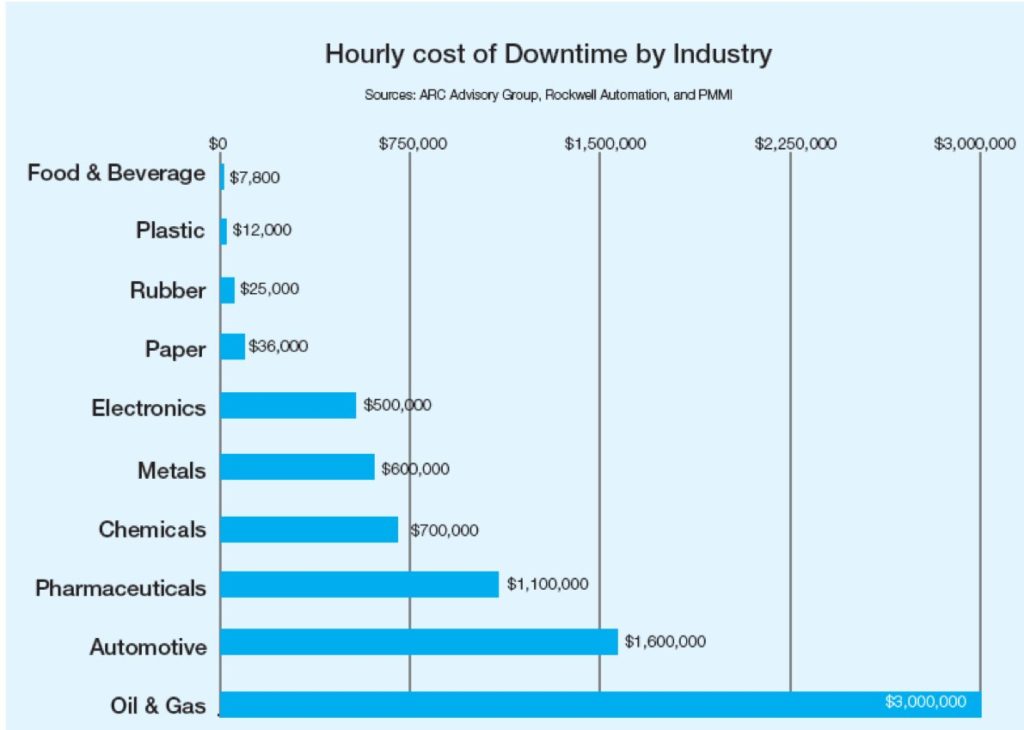
Inoltre, se si danneggia o rompe il cilindro per l’apertura e la chiusura della porta di carico, nel caso specifico di cui stiamo parlando (di un altoforno di medie dimensioni), ci vogliono circa 4 giorni per raffreddare il forno, 1 giorno di manutenzione per la sostituzione del pezzo ed altri 3 giorni per riavviare il forno.
Questo fa capire quanto sia importante preventivare una manutenzione in modo corretto ed avere componenti (anche pneumatici) molto affidabili.
Avere bene in mente i costi provocati da un fermo, fa comprendere fino in fondo l’importanza della manutenzione e della sicurezza dovuta all’affidabilità di macchine e singoli componenti. Non va quindi sottovalutata la questione: vediamo ora le peculiarità dei componenti pneumatici per il metallurgico.
Pneumatica ad alta affidabilità e resistenza
Le applicazioni pneumatiche per il metallurgico devono tenere in considerazione le caratteristiche dell’ambiente di lavoro di questo settore, ed essere quindi progettate di conseguenza.
Spesso le soluzioni che si progettano sono costruite su misura per le particolari esigenze dei diversi clienti, con un occhio di riguardo alle temperature estreme, alle alte pressioni e carichi, agli urti e ai fluidi aggressivi.
Un altro occhio di riguardo va alle impurità del metallo fuso e rovente, che schizzano e si possono posare sull’asta.
Se questo accade si possono fondere e creare una gobbetta che durante la corsa andrebbe a distruggere la guarnizione, andando così a compromettere la funzionalità del cilindro pneumatico.
Sono queste alcune caratteristiche delle quali non si può non tenere conto in fase di progettazione e che portano alla scelta di materiali speciali e molto resistenti per garantire una vita più lunga ed una maggiore affidabilità al cilindro.
Le dure condizioni alle quali il cilindro pneumatico non si piega (se ben costruito)
Abbiamo precedentemente elencato i problemi che un cilindro pneumatico potrebbe affrontare in questo ambiente di lavoro, ora vediamo come deve essere costruito per riuscire a lavorare a lungo, senza creare un danno all’azienda.
Per risolvere il problema di residui e scorie roventi che possono compromettere la qualità superficiale dello stelo, Cy.Pag. ha adottato una guaina, cappuccio di protezione, con un filtro dell’aria strategicamente posizionato, così da evitare di danneggiare il cilindro.
Inoltre viene applicato un raschia stelo con lamelle metalliche, che ha la funzione di rimuovere eventuali impurità e pulire l’asta da polvere o incrostazioni dure: ciò garantisce una vita più lunga al cilindro.
Un altro problema sono le temperature estreme che si raggiungono, che possono essere dannose soprattutto sulle guarnizioni: la gomma infatti si “smolla”, cuoce o diventa vetro.
Il Viton, usato da Cy.Pag., contiene fluoro che permette di mantenere la funzione elastica della guarnizione. Questo, unito ad elementi schermanti in PTFE o metallo permette di attenuare l’effetto delle alte temperature, permettendo così l’utilizzo dei cilindri anche con picchi di temperatura fino a oltre 200°C.
L’applicazione reale non è un test di laboratorio
Un nostro cliente mantiene operativo un forno per la lavorazione di metalli ad alte temperature, dove il cilindro pneumatico (come anticipato precedentemente) viene utilizzato per aprire e chiudere una porta di 4 quintali per permettere al carrello di far entrare ed uscire dal forno i metalli.
Per questa applicazione è stato progettato un cilindro diametro 320mm e corsa 1450mm, con stelo prolungato e guarnizioni in Viton.
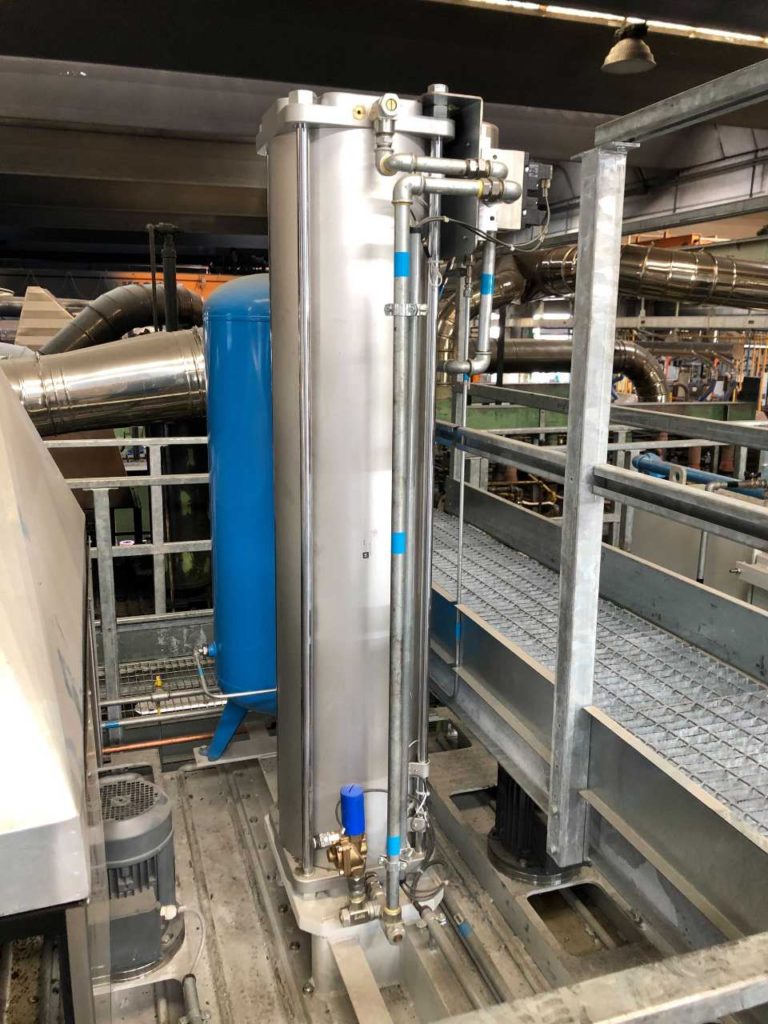
Dopo vari test e piccole migliorie, come l’aggiunta di uno schermo di protezione della guarnizione, il cilindro è finalmente stato montato ed è entrato in funzione.
I nostri cilindri per il metallurgico, comparati a quelli della concorrenza, sono più pesanti (che per queste applicazioni è un plus), più affidabili nel medio e lungo periodo, sopportano meglio i lavori gravosi e nonostante tutto riescono anche a mantenere un prezzo più competitivo grazie ad un mix di accorgimenti del nostro ufficio tecnico.
Se anche tu hai un’impresa che lavora in questo settore, oppure ti occupi della gestione o manutenzione di questo tipo di impianti non esitare a contattarci per sapere qualcosa di più su come possiamo migliorare la tua vita semplificando e riducendo le operazioni di manutenzione, con un cilindro più affidabile nel tempo.
Chiamaci al numero +39 0342 60 50 11 oppure scrivici una mail a info@cypag.com per richiedere una consulenza gratuita.